Disturbedfuel15
New Member
Hello,
It appears I pulled a rookie-move and had my JK PB2A16s20p balancing turned on when the cells were at 70%, where they came from the factory. I didn't realize I was possibly doing harm... now I know. In any case, I have five of these BMS, five 48v 280ah packs. The cells are laser-welded together, so I cannot remove them and connect all batteries in parallel to pursue the recommended top balance settings. I'm also using two SI6048US on the latest firmware. They are talking to the BMS pretty well for the most part. I have the battery type as external lithium ion, so it gets all charging parameters from the BMS (I believe).
There are a few cells in a couple packs that charge faster than others, causing the charging to stop due to cell OVP.
What I've read is that nowadays with active balancers, like these have, with 2a balancing current, I may be able to top balance by just letting the BMS' do their thing. I don't know that I can make the SIs send a constant charge voltage, so I have a 10a 0-60v bench power supply coming, too. If I don't have to open it and I can return it, that would be terrific. I'd like to top balance using the SIs.
I'll post my current BMS settings here. The only difference I made this morning before posting is I upped the requested charge voltage to 3.5v from 3.45v, and I set the charge current max at 2.0a in hopes the cells don't drift too far apart under this smaller charge current. Looking at the BMS displays currently, I'm seeing between 1-2a of current, so the BMS are doing their job. Once all cells reach 3.5v and are within .0010v of eachother, I want to up it to 3.55v, then 3.6v, and then maybe call it good? How does that sound? I appreciate any responses tremendously. I'm here to learn. Thank you!
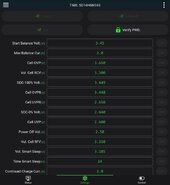
It appears I pulled a rookie-move and had my JK PB2A16s20p balancing turned on when the cells were at 70%, where they came from the factory. I didn't realize I was possibly doing harm... now I know. In any case, I have five of these BMS, five 48v 280ah packs. The cells are laser-welded together, so I cannot remove them and connect all batteries in parallel to pursue the recommended top balance settings. I'm also using two SI6048US on the latest firmware. They are talking to the BMS pretty well for the most part. I have the battery type as external lithium ion, so it gets all charging parameters from the BMS (I believe).
There are a few cells in a couple packs that charge faster than others, causing the charging to stop due to cell OVP.
What I've read is that nowadays with active balancers, like these have, with 2a balancing current, I may be able to top balance by just letting the BMS' do their thing. I don't know that I can make the SIs send a constant charge voltage, so I have a 10a 0-60v bench power supply coming, too. If I don't have to open it and I can return it, that would be terrific. I'd like to top balance using the SIs.
I'll post my current BMS settings here. The only difference I made this morning before posting is I upped the requested charge voltage to 3.5v from 3.45v, and I set the charge current max at 2.0a in hopes the cells don't drift too far apart under this smaller charge current. Looking at the BMS displays currently, I'm seeing between 1-2a of current, so the BMS are doing their job. Once all cells reach 3.5v and are within .0010v of eachother, I want to up it to 3.55v, then 3.6v, and then maybe call it good? How does that sound? I appreciate any responses tremendously. I'm here to learn. Thank you!
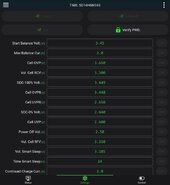