Hello,
I'm swapping out my 2x lead acid batteries on my trailer with 3x Lifepo4 batteries (and adding a shunt/inverter), and I wanted to get some input. The trailer currently has 8 AWG wire going from the battery (positive) to the disconnect. I am wanting to add a 2000 watt inverter. From what I've read online, I should use 2/0 wire. My questions are:
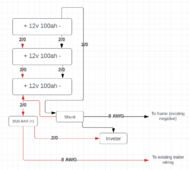
I'm swapping out my 2x lead acid batteries on my trailer with 3x Lifepo4 batteries (and adding a shunt/inverter), and I wanted to get some input. The trailer currently has 8 AWG wire going from the battery (positive) to the disconnect. I am wanting to add a 2000 watt inverter. From what I've read online, I should use 2/0 wire. My questions are:
- I need to use 2/0 wire between each battery, to the shunt, and to the inverter, correct? I've read conflicting suggestions of being able to use 1/0 or 2 AWG. I'll only be using this to charge laptops and occasionally make coffee.
- I've read that all of the cable lengths should be the same between the batteries. Can I use 1' between each battery, but then 2' or 3' from the negative terminal to the shunt (due to space issues the batteries have to be oriented as they are in my diagram). Should I use the same length from the final positive lead to the bus bar?
- Can I use 8 AWG to then run to the existing wiring in my trailer (negative to the frame and positive to the disconnect)?
- Can I connect the 2/0 wire and the 8 AWG to the trailer to the end of the shunt, or does this need to have a bus bar?
- Is there anything incorrect, wrong or missing in my plan? I know it's probably ideal to add a fuse between the bus bar and the inverter.
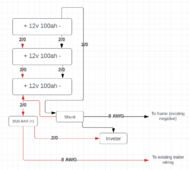