I have 4 - AOLITHIUM 51.2v 100ah Server Rack Lithium LiFePO4 Battery. In the manual its not clear on how to make all 4 communicate with “Pylontech”. All it says is jumper 32 (which is DIP 6-on) has to be set. It also is not clean if “slave 0” would be considered the first battery. Can someone help me on which jumpers have to be set to uses all 4 batteries. They informed me the the “CAN” port and the “RS485” port are invertchangable. I can use either port. 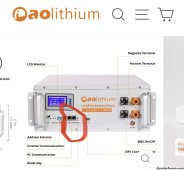
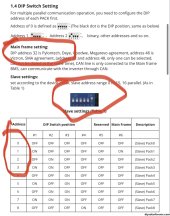
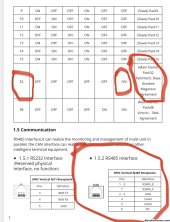
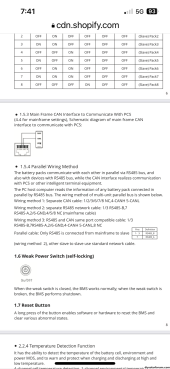
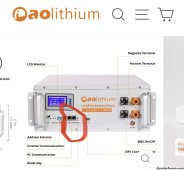
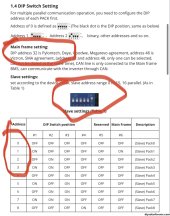
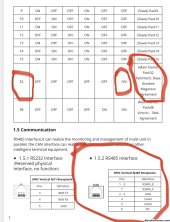
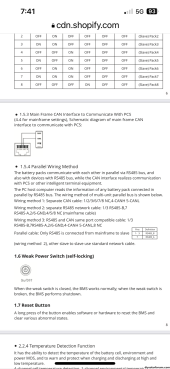