BillCaswell
New Member
- Joined
- Jan 10, 2020
- Messages
- 78
Hello all,
The Fortune 100Ah 3.2V 6C battery cell has been receiving good recommendations around the internet including on the Will Prowse DIY Solar Power YouTube channel. Checking the specs on the website www.electriccarpartscompany.com website lists some of the specs as "2C (6C for 10 seconds)." I am having a hard time finding a BMS that will work at 600 amps. Any suggestions?
A little back ground. I am replacing the 8D size, 24 volt AGM battery house bank system that is 2S/2P consisting of 12volt batteries from my sailboat. The house bank is also used to run the 20hp bow thruster electric motor. Typically the bow thruster is used in 3-5 second bursts. My challenge is that the running current is approximately 600 amps with an inrush current of 2-3x 1200-1800 for a few tenths of a second. For reasons that have to do with how the boat is configured, I need to keep powering the bow thruster using the house bank. See below for a picture of the battery box (basement) that I have to work with.
I have room in the battery box for 96 of these Fortune 100Ah LFP cells. If this helps, the battery box is
Battery Box
L: 47 1/4” (1,200.15 mm)
W: 22 1/4” (565.15 mm)
H: 21” (533.4 mm)
I am still working out how to organize the cells but could use any arrangement that provides 24 volts.
Two questions:
(1) Is there a recommendation on how to arrange the cells?
(2) Which BMS(s) do you recommend I look at? It needs to support the 6C pull for 10 secs.
Sources of charging include engine driven 220A Balmar alternator, 17.5 kWh generator and soon 1,000 watts of solar.
Thanks in advance. I hope that asking these types of questions are in bounds for this forum thread?
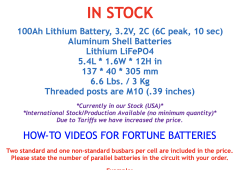

The Fortune 100Ah 3.2V 6C battery cell has been receiving good recommendations around the internet including on the Will Prowse DIY Solar Power YouTube channel. Checking the specs on the website www.electriccarpartscompany.com website lists some of the specs as "2C (6C for 10 seconds)." I am having a hard time finding a BMS that will work at 600 amps. Any suggestions?
A little back ground. I am replacing the 8D size, 24 volt AGM battery house bank system that is 2S/2P consisting of 12volt batteries from my sailboat. The house bank is also used to run the 20hp bow thruster electric motor. Typically the bow thruster is used in 3-5 second bursts. My challenge is that the running current is approximately 600 amps with an inrush current of 2-3x 1200-1800 for a few tenths of a second. For reasons that have to do with how the boat is configured, I need to keep powering the bow thruster using the house bank. See below for a picture of the battery box (basement) that I have to work with.
I have room in the battery box for 96 of these Fortune 100Ah LFP cells. If this helps, the battery box is
Battery Box
L: 47 1/4” (1,200.15 mm)
W: 22 1/4” (565.15 mm)
H: 21” (533.4 mm)
I am still working out how to organize the cells but could use any arrangement that provides 24 volts.
Two questions:
(1) Is there a recommendation on how to arrange the cells?
(2) Which BMS(s) do you recommend I look at? It needs to support the 6C pull for 10 secs.
Sources of charging include engine driven 220A Balmar alternator, 17.5 kWh generator and soon 1,000 watts of solar.
Thanks in advance. I hope that asking these types of questions are in bounds for this forum thread?
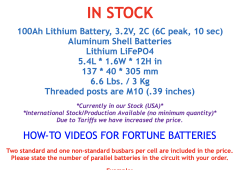
