paulsteigel
New Member
My Inverter prefer fix charge voltage. I observed some dedicated BMS shipped with whole pack of high quality battery over months connected to the inverter via Rs485 and it only applies a single voltage 56V during the charging and sometime does resetting SOC by trying to lengthen the charging process to make cell be as close to 3.45 as better. Over a year, I could hardly see the min cell voltage drop below 3.1V and few time discovered the max voltage reach 3.46.Hi @paulsteigel, the existing auto charge current control does similar to this already.
At the moment, we're working on controlling charge current through dynamically adjusting the requested CVL. That's the more effective way to do it, assuming your inverter regulates CVL properly...
The only things I found was changing of charging current limit.
The reason I moved to map function was the "High voltage warning" by the inverter. For the case of 280Ah battery pack, charging current reached 70-80A and make the cells become so unbalanced and current dropped a bit too quickly and make cells became less unbalanced. As the result the current get back high again.
I tested today with map(), current changed a bit slower comparing to yours great function (both in increasing and decreasing as well). My trick was defining a buffer such as 50mV toward the OVP (defined by user, not by the BMS and often 3450mV) and 10mV above the OVP. So when max_cell_volt increased as closer to the OVP the current will be mapped down from the initial charging current defined by user often 0.25 - 0.3C.
I used old code of Sleeper85 and revised quite remarkably to meet with Luxpower SNA5000. If tomorrow test is successful I will share back!
I learned from you alot by using the platform: copy. Before I have to rely on script.
In general, my approach is to help Inverter treating battery pack as lead acid.
I have small problem occurred today that Inverter complained "Battery High voltage" with one of my friend (SNA5000 but it does not happen with a SNA6000 of the same yaml code) when he charge with 50A current so he turn back to Lead acid and charge went well again using 57.5V without problem. So I doubt there would be problem relating to the reporting of charging voltage from BMS (CAN_ID 0x356) or (CAN_ID 0x351). I discussed with Luxpower Dealer on this point but he failed to explain (he might not know about this).
This is today record of the premium BMS with SVE5000WM battery
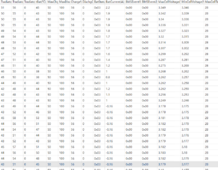
And this is today charging using map() for 50Ah battery
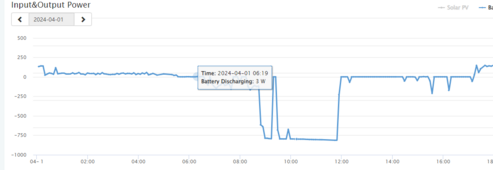
And this is today charge using your power() option with manual control of charging current
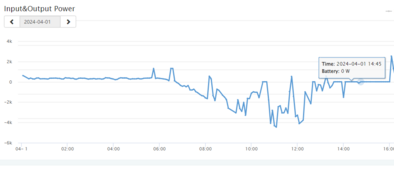
Last edited: