For my DIY power bank build I planned on utilyzing large Anderson SB175 to connect between two separate toolboxes (one housing chargers and the other holding a 230ah 12v battery and 2000w psw inverter). I'm using Windy Nation 2AWG welding cable and some Powerwerx #2 Anderson connectors for the Anderson SB175 housings. My first attempt at constructing the connection cables has left me with questions and wishing to hopefully obtain some helpful hints.
First attempt at stripping the cable ended badly (cut some shreds and tore the heat shrink) but by the second try I was getting good cuts and stripping. Then I attempted crimping the connectors and they came out of the hydraulic hand crimper distorted but seemingly tight with a good crimp that was holding. Got some heat shrink over the connector and cable and then found I couldn't insert the connector lug into the SB175 housing. Seems I need 3 hands to hold the housing, insert the lug and cable, and depress the springy housing contact. After many attempts at insertion, the crimp began to fail. I suspected the distortion of the lug was enough to prevent the combination from traveling inside the housing and seating properly. (I experimented and was easily able to insert and then remove an uncrimped/unheat-shrunk lug into the SB175 housing without any problem.) So, I decided to remove some of the distorted metal from the crimp and was able to fit the lug into the connector sans heat-shrink. I did have to screw the housing down to get better leverage while inserting the connector and I think that will also help to keep the cable from bending near the lug and maintain the crimp strength.
I'm assuming that isn't a best practice so looking for advise on how to fit everything together. I've attached a pic of the two cable ends with crimped connections. One shows how I removed some of the protruding metal and sanded it down to the copper. My questions include whether it is OK to insert these crimped and sanded connectors into the housings without using heat shrink on them or at least just where the cable meets the connector? Would vinyl electric tape be an acceptable substitute? Is the bared copper a problem and should I use some anti-corrosion gel on them to help prevent oxidation? And, am I overdoing the crimp? Should those connector lugs distort so much or would a lesser crimp pressure be sufficient? And finally, should the connector lug be oriented any certain way in the crimper so the resulting flat part of the crimp lines up with the blade or should it be at a different angle/perpendicular?
I'll attach a pic of the crimped lugs. One end shows the extent of the crimp (crimped 3 times over the length of the lug) and the other shows a more even shape after sanding it down a bit.
TIA for any guidance and tips you can provide.
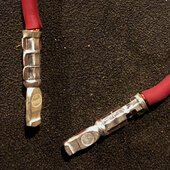
First attempt at stripping the cable ended badly (cut some shreds and tore the heat shrink) but by the second try I was getting good cuts and stripping. Then I attempted crimping the connectors and they came out of the hydraulic hand crimper distorted but seemingly tight with a good crimp that was holding. Got some heat shrink over the connector and cable and then found I couldn't insert the connector lug into the SB175 housing. Seems I need 3 hands to hold the housing, insert the lug and cable, and depress the springy housing contact. After many attempts at insertion, the crimp began to fail. I suspected the distortion of the lug was enough to prevent the combination from traveling inside the housing and seating properly. (I experimented and was easily able to insert and then remove an uncrimped/unheat-shrunk lug into the SB175 housing without any problem.) So, I decided to remove some of the distorted metal from the crimp and was able to fit the lug into the connector sans heat-shrink. I did have to screw the housing down to get better leverage while inserting the connector and I think that will also help to keep the cable from bending near the lug and maintain the crimp strength.
I'm assuming that isn't a best practice so looking for advise on how to fit everything together. I've attached a pic of the two cable ends with crimped connections. One shows how I removed some of the protruding metal and sanded it down to the copper. My questions include whether it is OK to insert these crimped and sanded connectors into the housings without using heat shrink on them or at least just where the cable meets the connector? Would vinyl electric tape be an acceptable substitute? Is the bared copper a problem and should I use some anti-corrosion gel on them to help prevent oxidation? And, am I overdoing the crimp? Should those connector lugs distort so much or would a lesser crimp pressure be sufficient? And finally, should the connector lug be oriented any certain way in the crimper so the resulting flat part of the crimp lines up with the blade or should it be at a different angle/perpendicular?
I'll attach a pic of the crimped lugs. One end shows the extent of the crimp (crimped 3 times over the length of the lug) and the other shows a more even shape after sanding it down a bit.
TIA for any guidance and tips you can provide.
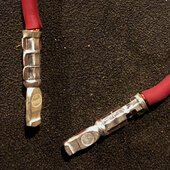
Last edited: