Frank in Thailand
making mistakes so you don't have to...
I have 3 x jikong BMS, 200A 2A balancing, on 3 x 260Ah BYD 51.2v battery packs (actually 6* S8)
"Identical" as can be, all with the same cable length.
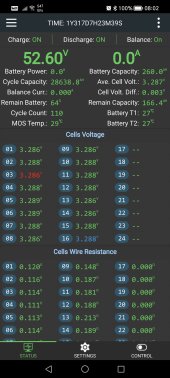
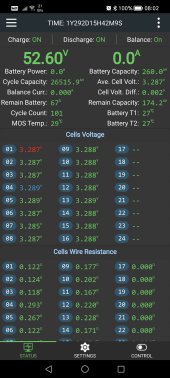
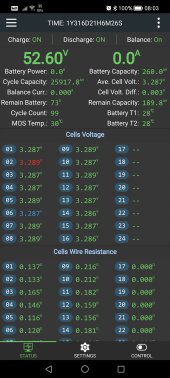
As you can see the cycle capacity is not the same.
My best explanation is that the total resistance per battery set is slightly different.
I also needed to adjust the voltage at start between the 3 BMS.
That's why there is a "calibrating voltage" setting
Use a reliable multimeter and test with the packs balanced and in rest.
Correct any offset... Done.
I've noticed that some of the 6 units charge a tad faster then the others, giving it some difference.
Nothing crazy.
Again, in my humble opinion..
Minor internal resistance difference.
I used a torque meter to have the terminals clamped with the same compression, yet...
So many things might give a slightly better or worse contact, different resistance.
10% cycle count difference is a "lot".
Yet..
In 2 years roughly 125 cycles per set.
Lithium is built for +3000 cycles
Or roughly after 50 years this would become an issue?
So I don't mind.
For OP..
As most suggested...
Start top balancing first!
Don't be a wuss...
Take your time for this.
If you are (like most) are charging on solar..
Your balanced pack should look like this in the early morning, before charging.. (so after +5 hours rest)
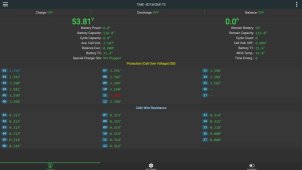
(Yes, Thailand it's dark at 19.00)
(Yes, my friend who made this screenshot should have been sleeping at 02AM ?)
Anyways...
This is what a good top balanced pack looks like.
He wasn't in hurry, and accepted that the absorption will take a DAY(!!) (Or more) to have a really good top balanced pack.
Once both sets are balanced...
measure the voltages with a multimeter.
Probably the same.
If not, check your connections..
some might be less optimal.
And please let us know how it is progressing!!
"Identical" as can be, all with the same cable length.
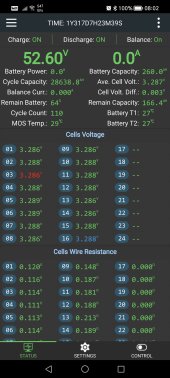
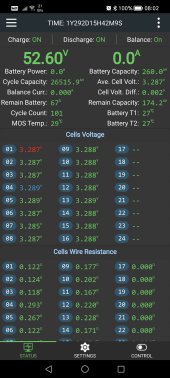
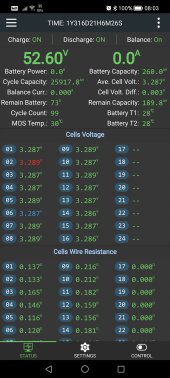
As you can see the cycle capacity is not the same.
My best explanation is that the total resistance per battery set is slightly different.
I also needed to adjust the voltage at start between the 3 BMS.
That's why there is a "calibrating voltage" setting
Use a reliable multimeter and test with the packs balanced and in rest.
Correct any offset... Done.
I've noticed that some of the 6 units charge a tad faster then the others, giving it some difference.
Nothing crazy.
Again, in my humble opinion..
Minor internal resistance difference.
I used a torque meter to have the terminals clamped with the same compression, yet...
So many things might give a slightly better or worse contact, different resistance.
10% cycle count difference is a "lot".
Yet..
In 2 years roughly 125 cycles per set.
Lithium is built for +3000 cycles
Or roughly after 50 years this would become an issue?
So I don't mind.
For OP..
As most suggested...
Start top balancing first!
Don't be a wuss...
Take your time for this.
If you are (like most) are charging on solar..
Your balanced pack should look like this in the early morning, before charging.. (so after +5 hours rest)
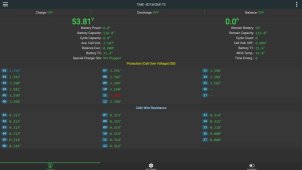
(Yes, Thailand it's dark at 19.00)
(Yes, my friend who made this screenshot should have been sleeping at 02AM ?)
Anyways...
This is what a good top balanced pack looks like.
He wasn't in hurry, and accepted that the absorption will take a DAY(!!) (Or more) to have a really good top balanced pack.
Once both sets are balanced...
measure the voltages with a multimeter.
Probably the same.
If not, check your connections..
some might be less optimal.
And please let us know how it is progressing!!
Last edited: