Have a look at the pictures i have attached, BMS/balancer cable is on a separate connection on the busbar, not connected at the terminals.So wait.. you spliced the cables ?
Battery terminal > crush ring > busbar > ring connector from PCB > (ring need BMS) > curated nut .. is what I used a few times before I drilled extra holes in busbar and never had any issues with that, although for safety the torque on all nuts is checked every year , and changed to drilled hole.
You do realize this BMS calculates resistance to cells amongst other things on every pcd connection I hope ?
Would surprise me at all the splicing causes issues with that process
Both BMS and balancer shares PCB and cable to each busbar.
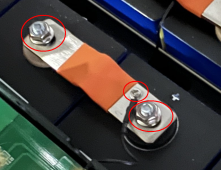