With the weather we get here (Northern Ireland) bottom end testing a solar storage system is easy. Today/Tomorrow I should get some top end testing done.
This was my first bottom end test of the 4S 105Ah LFP (Varicore) cells.
It's "as is". Open to interpretation. I'll give mine, but I others with experience will know more than I about how good, bad or terrible it actually is in the grander scheme of things.
snapshots.raintank.io
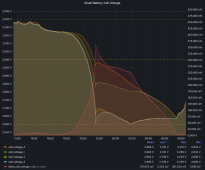
I just didn't turn the loads off when I would normally do so. I just let it run until the BMS proved it would do as it should.
The highlights in the first half are:
* just how steep that "cliff" becomes below whatever voltage. We knew this.
* the absolutely shocking state of the bottom "balance" or lack of it on these cells.
* The BMS does indeed kill discharge instantly (by the graph resolution/sampling) at 2.599V
The second part is more interesting. Figuring I might as well test the balancer out, I set it to "Always on" with a 5mV tolerance and left it to see what happened. The worst case in my view at the time was a cell would be pushed down to 2.5V and the BMS would shut itself off as well and I'd have to go out and reboot it in the morning.
That test, in my opinion, running the balancer at the bottom end was a complete failure on the BMS's part. It looks like it is "dumb round robin fly capacitor" balancing, going cell1, cell2, cell3, cell4. Unfortunately poor cell 3 never really gets his "fair" share of cell 4s excess and the balancer drives it into a LVC state again. It is at least reassuring a little that it did not simply repeat that mistake over and over.
In fairness, it did get the cells in balance just before dawn. However, I will be returning it's setting to upper top region only.
Unless I have good reason to or it happens by accident, it's probably the last time I produce a graph like this.
We have two days of sun, maybe today I will see what happens to that bottom balance when it reachs the top. I have no high expectations for these cells, but I expect the balancer to get a work out.
Other notes: The MPPT control did go off line given not even a few mA trickle from the BMS. When the BMS recovered at 2.65V the MPPT did power back up again normally. However during that second "BUMP" at 2.6V the MCU on the MPPT ModBus port crashed and did not recover, most likely brown out. Just data loss and monitoring glitch on the MPPT side. No biggy it was still functioning as an MPPT.
This was my first bottom end test of the 4S 105Ah LFP (Varicore) cells.
It's "as is". Open to interpretation. I'll give mine, but I others with experience will know more than I about how good, bad or terrible it actually is in the grander scheme of things.
Grafana

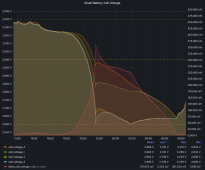
I just didn't turn the loads off when I would normally do so. I just let it run until the BMS proved it would do as it should.
The highlights in the first half are:
* just how steep that "cliff" becomes below whatever voltage. We knew this.
* the absolutely shocking state of the bottom "balance" or lack of it on these cells.
* The BMS does indeed kill discharge instantly (by the graph resolution/sampling) at 2.599V
The second part is more interesting. Figuring I might as well test the balancer out, I set it to "Always on" with a 5mV tolerance and left it to see what happened. The worst case in my view at the time was a cell would be pushed down to 2.5V and the BMS would shut itself off as well and I'd have to go out and reboot it in the morning.
That test, in my opinion, running the balancer at the bottom end was a complete failure on the BMS's part. It looks like it is "dumb round robin fly capacitor" balancing, going cell1, cell2, cell3, cell4. Unfortunately poor cell 3 never really gets his "fair" share of cell 4s excess and the balancer drives it into a LVC state again. It is at least reassuring a little that it did not simply repeat that mistake over and over.
In fairness, it did get the cells in balance just before dawn. However, I will be returning it's setting to upper top region only.
Unless I have good reason to or it happens by accident, it's probably the last time I produce a graph like this.
We have two days of sun, maybe today I will see what happens to that bottom balance when it reachs the top. I have no high expectations for these cells, but I expect the balancer to get a work out.
Other notes: The MPPT control did go off line given not even a few mA trickle from the BMS. When the BMS recovered at 2.65V the MPPT did power back up again normally. However during that second "BUMP" at 2.6V the MCU on the MPPT ModBus port crashed and did not recover, most likely brown out. Just data loss and monitoring glitch on the MPPT side. No biggy it was still functioning as an MPPT.