Old_Skewler
Solar Enthusiast
I am trying to wrap my head around the dynamics between a lithium rack-type battery with internal BMS and a inverter charger which has NO communication with the battery BMS.
Who dictates the charging current to feed the battery? The battery BMS or the inverter charger?
I ask this because I have the following conditions:
- Schneider 4048SW Inverter Charger set up to a max current of 35A.
When battery is at 58% SOC and I run the charger, the battery intakes 35A. Once the battery reaches 100% SOC, it still manages to intake about 30A from the charger, to which at the point I turn off the generator.
I have the following questions I would like to hear from other members:
1. who should be in "charge" (pun intended) of the charging current going to the battery: the battery BMS or the Inverter Charger?
2. What eventually would had happened if I didn't turn off the generator once the battery hit 100% SOC? Would the same 30A still try to get into the battery or would the battery say "enough is enough" and reduce the intake current? How does this actually work?
Here are some screenshots I took today during the beginning of the charge cycle SCO 58% and another screenshot at 100% SOC.
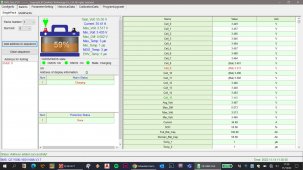
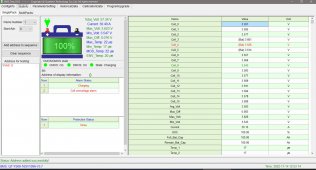
Who dictates the charging current to feed the battery? The battery BMS or the inverter charger?
I ask this because I have the following conditions:
- Schneider 4048SW Inverter Charger set up to a max current of 35A.
When battery is at 58% SOC and I run the charger, the battery intakes 35A. Once the battery reaches 100% SOC, it still manages to intake about 30A from the charger, to which at the point I turn off the generator.
I have the following questions I would like to hear from other members:
1. who should be in "charge" (pun intended) of the charging current going to the battery: the battery BMS or the Inverter Charger?
2. What eventually would had happened if I didn't turn off the generator once the battery hit 100% SOC? Would the same 30A still try to get into the battery or would the battery say "enough is enough" and reduce the intake current? How does this actually work?
Here are some screenshots I took today during the beginning of the charge cycle SCO 58% and another screenshot at 100% SOC.
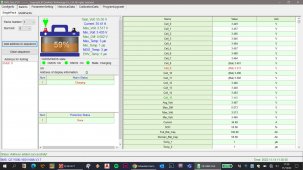
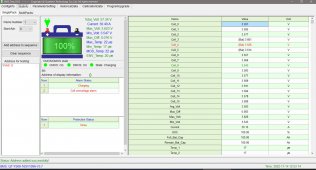