Hello folks, I’ve new to the forum and this is my first post after I got pointed in this direction by a member on a support forum for the Outback Inverters I’m using.
I have recently undertaken this project of adding battery backup to my current Enphase IQ7 AC coupled solar setup. This project started when I was offered a great price on these Chevy Bolt batteries that a friend of mine acquired and then reconfigured to 14s / 48v. I purchased 6 initially and soon to add two more..and will have a total of 8 packs which I plan to run in parallel to power my pair of Outback Radian 8048s.
In the process of reconfiguring this packs for 14s, the original balance connectors were disconnected, so I spent quite a bit of time with a soldering iron and 20g wire to create balance connectors for these packs and my original plan was to manually keep a close eye on these packs to make sure the cells stay balanced while they are being used. However, the more I ponder this, I would love to be able to plan and implement a BMS setup for these packs that I could trust to keep up with these packs and maybe even automatically shut of the inverter/charger if something is out of order with the cells.
In my searching and reading through this forum, it seems like this should be an option, but I would love to hear some ideas on what setup you guys would recommend for trying to accomplish my goals.
Im including some pictures of my batterie and how I created my balance tabs. My friend who got me into this whole project is using a very similar setup with his Victron Inverters and his batteries have stayed very well in balance now going on 2 months of use. So I’m hoping that with very conservative use of these batteries, that is keeping my cell voltages on the low and high end very conservative, I will have an even less likelyhood of the cells needing much if any balancing. For now I have a 2 A Active balancer that I could use to balance each pack individually if I need to.
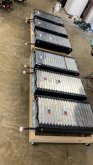
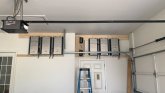
Video of me checking the cells with a battery checker
I have recently undertaken this project of adding battery backup to my current Enphase IQ7 AC coupled solar setup. This project started when I was offered a great price on these Chevy Bolt batteries that a friend of mine acquired and then reconfigured to 14s / 48v. I purchased 6 initially and soon to add two more..and will have a total of 8 packs which I plan to run in parallel to power my pair of Outback Radian 8048s.
In the process of reconfiguring this packs for 14s, the original balance connectors were disconnected, so I spent quite a bit of time with a soldering iron and 20g wire to create balance connectors for these packs and my original plan was to manually keep a close eye on these packs to make sure the cells stay balanced while they are being used. However, the more I ponder this, I would love to be able to plan and implement a BMS setup for these packs that I could trust to keep up with these packs and maybe even automatically shut of the inverter/charger if something is out of order with the cells.
In my searching and reading through this forum, it seems like this should be an option, but I would love to hear some ideas on what setup you guys would recommend for trying to accomplish my goals.
Im including some pictures of my batterie and how I created my balance tabs. My friend who got me into this whole project is using a very similar setup with his Victron Inverters and his batteries have stayed very well in balance now going on 2 months of use. So I’m hoping that with very conservative use of these batteries, that is keeping my cell voltages on the low and high end very conservative, I will have an even less likelyhood of the cells needing much if any balancing. For now I have a 2 A Active balancer that I could use to balance each pack individually if I need to.
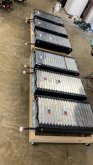
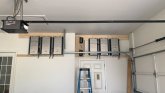
Video of me checking the cells with a battery checker