Hi again, I am seeking some clarification on design / install configuration for a 14kw PV with hybrid inverter and 30kwh battery storage.
I have a Cutler hammer HP404040SH with max rating of 400amps (pic below). It has a 200A service breaker "A" with main breaker panel that provides service to half the home including 3 A/C units. The main panel also has a 200A service panel "B" breaker that feeds a separate breaker panel at the other end of the house which also has 3 A/C units attached. The branch circuit stab max at 225Amps.
I am looking to peak shave for the entire house (therefore whole house backup required) and seeking to reduce peak hour usage by 75% in hottest months (i.e. 10kwh down to 3kwh).
Based on the above, I do have a few questions:-
a) What installation configuration do I need? Supply side or feeder tap? What is the modification to the standard EG4 (fig 4.3) or Sol Ark install to accommodate the 2 branches?
b) How can I uprate the system to allow more than 40Amps to be backfed?
c) In a supply side or feeder tap, if the inverter fails (EG4 18kpv or SolArk 15k) will grid supply to the house be automatically shut down? I see the call for a manual transfer switch but that isn't useful if you are not home.
d) My peak hourly load is over 20kw (so this is not instantaneous peak), is there any danger in overloading the inverter with grid pass through?
Any other look outs in what I am doing?
Thanks in advance
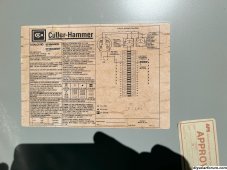
I have a Cutler hammer HP404040SH with max rating of 400amps (pic below). It has a 200A service breaker "A" with main breaker panel that provides service to half the home including 3 A/C units. The main panel also has a 200A service panel "B" breaker that feeds a separate breaker panel at the other end of the house which also has 3 A/C units attached. The branch circuit stab max at 225Amps.
I am looking to peak shave for the entire house (therefore whole house backup required) and seeking to reduce peak hour usage by 75% in hottest months (i.e. 10kwh down to 3kwh).
Based on the above, I do have a few questions:-
a) What installation configuration do I need? Supply side or feeder tap? What is the modification to the standard EG4 (fig 4.3) or Sol Ark install to accommodate the 2 branches?
b) How can I uprate the system to allow more than 40Amps to be backfed?
c) In a supply side or feeder tap, if the inverter fails (EG4 18kpv or SolArk 15k) will grid supply to the house be automatically shut down? I see the call for a manual transfer switch but that isn't useful if you are not home.
d) My peak hourly load is over 20kw (so this is not instantaneous peak), is there any danger in overloading the inverter with grid pass through?
Any other look outs in what I am doing?
Thanks in advance
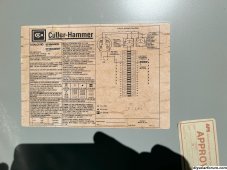