silverstone
Solar Enthusiast
- Joined
- May 3, 2022
- Messages
- 1,041
I usually use WAGO and Phoenix Contact Terminal Blocks.
I must say however that it's a bit opaque on their product catalogs and online product viewers, since it mostly says that those terminal blocks accept:
- Solid Conductors (Class 1)
- Stranded Conductors (Class 2)
- Fine-Stranded Conductors - With and/or Without Ferrules (Class 5)
Nothing is however said about Extra Fine-Stranded Conductors (Class 6). The WAGO Terminal Blocks come with a Pictogram that is very cryptic (3 wire types you can connect and 1 that you cannot, but not sure which is which).
Specifically I am looking at:
- WAGO 2016-1301
- WAGO 285-135
- WAGO 285-150
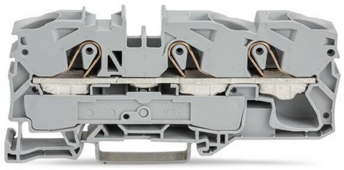

I am wondering about this, because the JK BMS B2A24S20P comes with what I believe are AWG7 Class 6 (Extra Fine Stranded) Tinned Copper Conductors.
I must say however that it's a bit opaque on their product catalogs and online product viewers, since it mostly says that those terminal blocks accept:
- Solid Conductors (Class 1)
- Stranded Conductors (Class 2)
- Fine-Stranded Conductors - With and/or Without Ferrules (Class 5)
Nothing is however said about Extra Fine-Stranded Conductors (Class 6). The WAGO Terminal Blocks come with a Pictogram that is very cryptic (3 wire types you can connect and 1 that you cannot, but not sure which is which).
Specifically I am looking at:
- WAGO 2016-1301
- WAGO 285-135
- WAGO 285-150
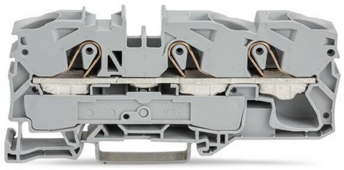

I am wondering about this, because the JK BMS B2A24S20P comes with what I believe are AWG7 Class 6 (Extra Fine Stranded) Tinned Copper Conductors.