Hello fellow electric wizards - one question I’m struggling to wrap my head around.
I’m sure it’s straight forward for someone.
I have x2 banks @24v (made up of eve 280amp lithium cells)
So that means x2 bms. (Overkill solar 24v)
One bank is very close to the
“all in one solar/inverter unit”
The other is 1.5m away.
Now to connect them right so they charge & draw balanced is the question: how ?
With one being close to the source other at a 1.5 m distance.
I’ve drawn a diagram to visually explain.
My confusion lies mainly with. The negative cable.
Do I connect both batterys togther via a solid negative wire. Direct from battery terminal to battery terminal.
Or do I Conect them via the output of the bms.
In my drawing I have option 1 on the left option 2 on the right.
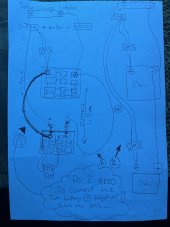
And yes I also have x1 shunt (not shown in drawing) where should attach the shunt ?
Assuming I’m planing on using the x1 shunt for both the batterys (treating both these batterys as a complete system) remaining 24v
Thanks in advance for your advice
I’m sure it’s straight forward for someone.
I have x2 banks @24v (made up of eve 280amp lithium cells)
So that means x2 bms. (Overkill solar 24v)
One bank is very close to the
“all in one solar/inverter unit”
The other is 1.5m away.
Now to connect them right so they charge & draw balanced is the question: how ?
With one being close to the source other at a 1.5 m distance.
I’ve drawn a diagram to visually explain.
My confusion lies mainly with. The negative cable.
Do I connect both batterys togther via a solid negative wire. Direct from battery terminal to battery terminal.
Or do I Conect them via the output of the bms.
In my drawing I have option 1 on the left option 2 on the right.
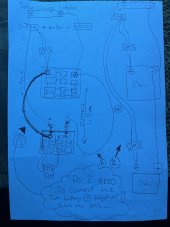
And yes I also have x1 shunt (not shown in drawing) where should attach the shunt ?
Assuming I’m planing on using the x1 shunt for both the batterys (treating both these batterys as a complete system) remaining 24v
Thanks in advance for your advice