kolek
Inventor of the Electron
- Joined
- Sep 29, 2021
- Messages
- 796
Nice idea but this would require making 2 new AWG 2/0 cables and forcing at least one of them to make 2 or 3 impossible 90 angles in 3 dimensions. The wires connecting my busbar to my 200A DC breaker are only about 4 inches long. It would be a lot easier for me to do scenario #2 above (meaning inverter on opposite ends and batteries in the middle), assuming there's any actual benefit to making the change.Busbar seems pretty short, but why not put inverter in middle, one battery on either side, for perfect symmetry?
What is the consensus on how bad the current wiring setup is (shown again below) ? Seems like nobody knows for sure if this wiring order actually matters over the long haul.
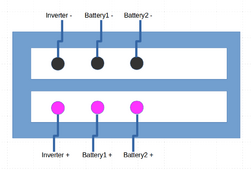
Last edited: