Arrived today so wanted to share with you initial unboxing on this Battery Equalizer PLC-10 from Mazava
Purchased from AliExpress for around $35, it looked to be exactly what I was looking for.
I have 4x12V in a 2P 2S setup for 24v. I have matched batteries but purchased at a different time (within a couple of months) and noticed a few anomalies with voltages so purchased this. I have however been running the Victron Balancer in the last couple of weeks as this was taking a while to arrive.
No issues with the Victron, but this is half the price and having the visible display means I need to pull out the multimeter less and can see where things are at at a glance. Also the Victron seems to only balance when there is around 150-200mV difference. The Victron also required the mid-points to be connected, something I still don't really understand but it did work!
Packaging is minimal to say the least, manual and unit, nothing else. Although not shown in the manual, this is designed to me mounted directly to a rail, it simply clips in. Wish they showed this in the manual, I need to buy a rail for this, but tested on one I have for my battery breaker and it works perfectly, just clips on.
Build quality does not seem amazing, but for the price I think that's to be expected and what counts is if it works.





For my setup, I figured I needed 2 of these, one for each pair of batteries. "The manual does state 'It can be connected to the battery connected in series for a long time to automatically maintain battery balance without maintenance." I have to say I am not sure what that means with regard to parallel batteries and if long term connection would cause issue? For not I have these connected full time.
Battery setup for Sealed is B03 (default), but can be changed easily to suit a wide range of batteries including lithium. However these are designed for 7-18Vdc.
The balancing current is up to 10A, compared to the Victron which was 0.7A.
The standby current is 7mA compared with the Victron 0.7mA (presumably due to the screen)
The way i connected is like this as per the manual:

End result is:

So far balancing is already good on my batteries, so this has come on for a short period only, however time will really tell how well this works. When balancing turns on an arrow comes on to show which way the balancer is moving current. I have no power meter yet but will give this a test after I have purchased one. One thing i have noticed is the Voltage reads a little higher than my multimeter. It basically seems to round it up as only goes to 1dp, or my multimeter may be off.
Cost is not actually much cheaper than the Victron after buying 2 at least for my setup, however love the fact I have a constant visualisation of battery voltages, and can see when its balancing. Also the balancing current of 10A is a major plus in terms of speed over the Victron.
Will feedback more as time goes on!
Purchased from AliExpress for around $35, it looked to be exactly what I was looking for.
I have 4x12V in a 2P 2S setup for 24v. I have matched batteries but purchased at a different time (within a couple of months) and noticed a few anomalies with voltages so purchased this. I have however been running the Victron Balancer in the last couple of weeks as this was taking a while to arrive.
No issues with the Victron, but this is half the price and having the visible display means I need to pull out the multimeter less and can see where things are at at a glance. Also the Victron seems to only balance when there is around 150-200mV difference. The Victron also required the mid-points to be connected, something I still don't really understand but it did work!
Packaging is minimal to say the least, manual and unit, nothing else. Although not shown in the manual, this is designed to me mounted directly to a rail, it simply clips in. Wish they showed this in the manual, I need to buy a rail for this, but tested on one I have for my battery breaker and it works perfectly, just clips on.
Build quality does not seem amazing, but for the price I think that's to be expected and what counts is if it works.





For my setup, I figured I needed 2 of these, one for each pair of batteries. "The manual does state 'It can be connected to the battery connected in series for a long time to automatically maintain battery balance without maintenance." I have to say I am not sure what that means with regard to parallel batteries and if long term connection would cause issue? For not I have these connected full time.
Battery setup for Sealed is B03 (default), but can be changed easily to suit a wide range of batteries including lithium. However these are designed for 7-18Vdc.
The balancing current is up to 10A, compared to the Victron which was 0.7A.
The standby current is 7mA compared with the Victron 0.7mA (presumably due to the screen)
The way i connected is like this as per the manual:

End result is:
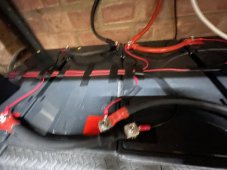

So far balancing is already good on my batteries, so this has come on for a short period only, however time will really tell how well this works. When balancing turns on an arrow comes on to show which way the balancer is moving current. I have no power meter yet but will give this a test after I have purchased one. One thing i have noticed is the Voltage reads a little higher than my multimeter. It basically seems to round it up as only goes to 1dp, or my multimeter may be off.
Cost is not actually much cheaper than the Victron after buying 2 at least for my setup, however love the fact I have a constant visualisation of battery voltages, and can see when its balancing. Also the balancing current of 10A is a major plus in terms of speed over the Victron.
Will feedback more as time goes on!
Attachments
Last edited: