lukemiller
New Member
- Joined
- Feb 27, 2021
- Messages
- 6
I'm trying to decide if I should build my own busbars (for higher ampacity) or if the bars that came with my 230AH cells are worth using. I'm noticing conflicting calculators (top 2 google results) and wondering if anyone can help explain the differences:
This site lists a 1/8 by 3/4 copper bar at 215A:
www.copper.org
This calculator has 1/8 by 3/4 copper bar at 72A:
www.electrical4u.net
I know voltage drop and temp could effect ratings, but the two are pretty dramatically different. I'm leaning towards the lower number, chart #1 doesn't even seem to be calculating area correctly...
Included busbars are 2 stacked .75mm by 20mm wide, I think they are galvanized. By calculator #2 they can support somewhere around a wopping 18A. Well short of the 150A rating I'm looking for.
This site lists a 1/8 by 3/4 copper bar at 215A:
Electrical: Busbar - DC Copper Busbar Ampacities
The following tables have been provided by the Alliance for Telecommunications Industry Solutions (ATIS), T1 Committee, and represent ampacities for busbar sizes and arrangements typically found in the telecommunications industry.

This calculator has 1/8 by 3/4 copper bar at 72A:
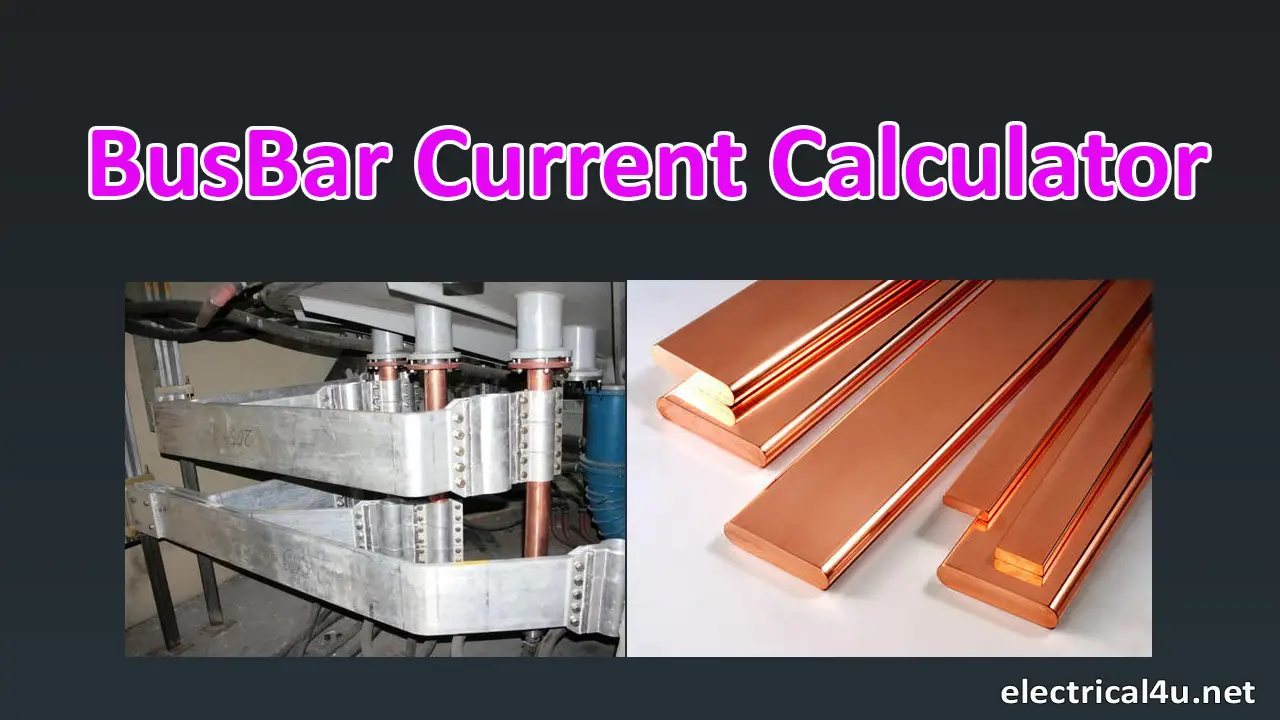
Busbar Current Calculator Online | Electrical4u
Enter the breadth and thickness of the busbar; do not enter the length of the busbar. Then press the calculate button, you get the aluminium or copper busbar

I know voltage drop and temp could effect ratings, but the two are pretty dramatically different. I'm leaning towards the lower number, chart #1 doesn't even seem to be calculating area correctly...
Included busbars are 2 stacked .75mm by 20mm wide, I think they are galvanized. By calculator #2 they can support somewhere around a wopping 18A. Well short of the 150A rating I'm looking for.