ehahn
New Member
Assumptions:
I understand LiFePO4 has a low internal resistance, so when you hook it up to an internally regulated alternator, the voltage differential from the battery and alternator divided by the battery’s low internal resistance causes a massive spike in current. The alternator quickly reaches max output and the alternator voltage drops such that ohms law is satisfied for the charging circuit. With a large enough battery bank, the input current isn’t a big deal for the LiFePO4. However, running the alternator at max output can cause the alternator to overheat, therefore we need a way to drop its output voltage and therefore output power to keep it from overheating (a classical duty of an external regulator). As long as you can keep it from overheating, you can continue to charge albeit at a limp output, but so far all seems well. The alternator will produce all it can until the battery pack is charged enough to allow the alternator to hit its max regulated voltage, at which point the voltage differential between the alternator and the battery will begin to decrease and therefore the circuit current will begin to decrease as the LiFePO4 continues to complete its constant voltage charge stage. As long as the BMS has overcharge protection, the battery will accept charge until full.
Question:
What am I missing? It seems with all the parameters correctly configured, the only thing I need to charge LiFePO4 off of an alternator is a way to regulate alternator temperature?
Another question. Is it possible that the BMS gets confused about when to deny charge when the battery is charging at the same time it’s under load? How does the BMS prevent overcharging? Does it disconnect the circuit completely, or maybe insert a diode into the circuit such that the battery can only discharge until the circuit voltage drops below the battery open circuit voltage?
Why ask?
Because I discovered a company claiming to make alternators with internal regulators that also are smart enough to regulate temperature
www.dcpowerinc.com
And I’m wondering if I can cut a lot of complexity and cost out of converting an alternator to external regulation, wiring up an external regulator, current shunts, SOC measurement, temperature sensors, meh - I hope I can just drop this thing in.
I understand LiFePO4 has a low internal resistance, so when you hook it up to an internally regulated alternator, the voltage differential from the battery and alternator divided by the battery’s low internal resistance causes a massive spike in current. The alternator quickly reaches max output and the alternator voltage drops such that ohms law is satisfied for the charging circuit. With a large enough battery bank, the input current isn’t a big deal for the LiFePO4. However, running the alternator at max output can cause the alternator to overheat, therefore we need a way to drop its output voltage and therefore output power to keep it from overheating (a classical duty of an external regulator). As long as you can keep it from overheating, you can continue to charge albeit at a limp output, but so far all seems well. The alternator will produce all it can until the battery pack is charged enough to allow the alternator to hit its max regulated voltage, at which point the voltage differential between the alternator and the battery will begin to decrease and therefore the circuit current will begin to decrease as the LiFePO4 continues to complete its constant voltage charge stage. As long as the BMS has overcharge protection, the battery will accept charge until full.
Question:
What am I missing? It seems with all the parameters correctly configured, the only thing I need to charge LiFePO4 off of an alternator is a way to regulate alternator temperature?
Another question. Is it possible that the BMS gets confused about when to deny charge when the battery is charging at the same time it’s under load? How does the BMS prevent overcharging? Does it disconnect the circuit completely, or maybe insert a diode into the circuit such that the battery can only discharge until the circuit voltage drops below the battery open circuit voltage?
Why ask?
Because I discovered a company claiming to make alternators with internal regulators that also are smart enough to regulate temperature
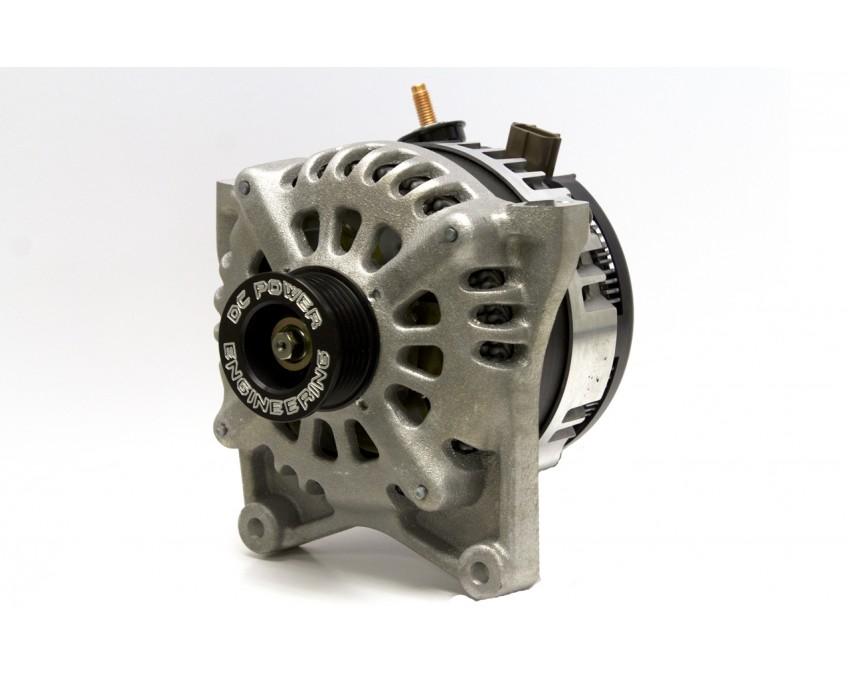
270 Amp XP High Output Alternator (Ford Expedition)
Our XP series high-output alternators are the ultimate upgrade when you need the absolute biggest and most sophisticated high output alternator on the planet. All of our XP series alternators are designed for one purpose, brute force idle output. When you need the most extreme idle output with...

And I’m wondering if I can cut a lot of complexity and cost out of converting an alternator to external regulation, wiring up an external regulator, current shunts, SOC measurement, temperature sensors, meh - I hope I can just drop this thing in.
Last edited: