Zakkieboy44
New Member
I think I have an idea on how to charge some spare Lead Acids along side my (new) setup but lack the expertise to know what components I'm talking about, so please bear with me whilst I explain my theory and get some wording wrong!
After reading that you shouldn't really mix battery types, and having a spare (nasty) charge controller I thought this route would work, as each controller is responsible for its own battery array. (1 x Lifepo4, 2 x Lead acid) -12v
My logic however is questioning the flow down into a single invertor - as I don't want any form of backflow from one battery to another, and after looking at blocking diodes there doesn't seem to be a 'consumer friendly' way to implement into the setup and im not 100% sure its the right tool for the job
I tried to draw a simplified layout, and would welcome any thoughts or feedback on the plan, and indeed what the names are of the 'bits' in the green circles that I would need to make this work - safely. (The picture doesn't show the fuses on the connections to the invertor)
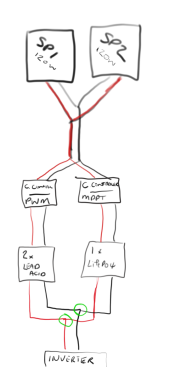
Id appreciate any feedback, however short - I have searched for a similar setup/situation, but my google skills seem to be failing me!
Thanks
Zak
After reading that you shouldn't really mix battery types, and having a spare (nasty) charge controller I thought this route would work, as each controller is responsible for its own battery array. (1 x Lifepo4, 2 x Lead acid) -12v
My logic however is questioning the flow down into a single invertor - as I don't want any form of backflow from one battery to another, and after looking at blocking diodes there doesn't seem to be a 'consumer friendly' way to implement into the setup and im not 100% sure its the right tool for the job
I tried to draw a simplified layout, and would welcome any thoughts or feedback on the plan, and indeed what the names are of the 'bits' in the green circles that I would need to make this work - safely. (The picture doesn't show the fuses on the connections to the invertor)
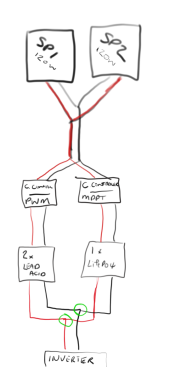
Id appreciate any feedback, however short - I have searched for a similar setup/situation, but my google skills seem to be failing me!
Thanks
Zak