Interesting, what's this controller?
Right from the beginning I've decided to make the system as safe as possible. Beside the passive things to do like
- mount everything on cement board
- using quality breakers on all relevant locations (PV, battery, AC-in, AC-out)
- oversize the cable cross sections - at least a bit
- be very accurate about battery screw torques
- using LiFePO4 batteries and no other lithium based chemistry because they can't thermally runaway
- using a thermal camera while a (nearly) full load test with batteries was running to check for bad connections (I was not able to do a full load test with the possible 39kW inverter power... I just don't have enough load for testing
- but I've tested with 24 kW)
- ...
I also wanted to integrate a security shutdown mechanism which should be triggered if one of the following situations occur:
- smoke detectors over the inverter wall will be activated
- an inside located emergency shutdown button was pushed
- an outside located emergency shutdown button was pushed
- remote via WiFi relay (via integration into my existing OpenHAB smart home system)
- if a camera will detect smoke or fire in the picture analysis (this was a later addon because it was easy to implement with my existing smart home and camera solutions)
I don't want to look paranoid, but nearly all of these AIO's are produced usually with cheap parts and unknown build quality. Our master bedroom is behind this inverter wall. We are living in the Mohave desert with usually less than 10 days rain per year and many days above >115 and even >120 Fahrenheit. In the event of a fire, a house here would burn down within minutes.
In case of an emergency (automatically detected or manually initiated) my goal was to cut all possible energy sources of the AIO's, which are
- solar PV
- batteries
- grid for optional charging the batteries (just an an backuP)
To disconnect the solar PV, I'm using the module based Tigo PVRSS system. The batteries are connected via 600A/80VDC relays (one per battery rack) which are normally open (NO relays). The grid is connected via two 3-pole 110A/240VAC contactors (3-pole is required because I'm using 3 AIO's per phase) and these contactors are also NO.
I also wanted to be able to disconnect all three of these energy sources remote via WiFi in case I would like to do this for whatever reason. Last but not least, the controller enclosing should be able to integrate the Rasperry Pi with SolarAssistant for monitoring of the batteries and remote controlling and monitoring of each individual AIO.
For all these requirements, I've designed and build a controller circuit. Because both the Kidde smoke detector controlling module and the Raspberry Pi getting pretty warm (beside some other parts), I've also installed a temperature controlled fan to cool the compartment of the controller. At the end, the controller consists out of about 13 relays (SSR-, WifFi and mechanical relays). The 600A battery relays need 48VDC to drive, the 110A AC-in contactors need 120VAC to drive, some other relays need 12VDC to drive, the Raspberry Pi needs 5VDC, so the controller has a 48VDC power supply and two buck converters create the 12VDC and 5VDC from it.
Because all 3 power sources are connected via NO relays (even the Tigo PVRSS), I need a blackstart UPS to power at least the controller circuit for a short time to "boot" the system.
It was a lot of work but also fun to design and build it. Now I can sleep with a better feeling and I know I've done a lot to reduce the risk of a disaster.
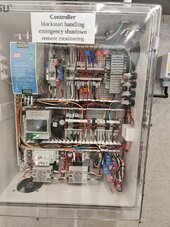