DerBuchner
New Member
- Joined
- Oct 5, 2022
- Messages
- 24
I have read various articles that one should not connect the components of a "solar system" directly, but that a pre-charge resistor must be used.
Sometimes I've seen that a connection is bridged by hand - temporarily - for a few seconds with a power resistor and only afterwards the actual cable is connected.
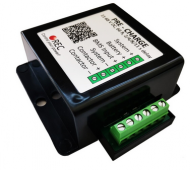
The explanation was, for example: When a device, like an inverter, is instantly connected to the battery, it is like a short circuit for the battery, which then supplies 100+ amps and kills the inverter. Because the capacitors suck themselves full and can't cope with it.
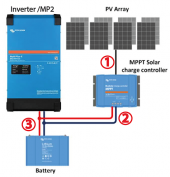
[edit] I forgot to mention: I intend to use a DIY LiFePO4 battery with 48 V and 14 kWh.
Question: Is such a pre-charge resistor really necessary or is this more like an urban myth?
(1) from the panels to the MPPT, I don't think so, a normal circuit breaker should suffice, right?
(2) at the connection MPPT <-> battery: do you need a pre-charge resistor here?
(3) at the connection battery <-> inverter: do you need a pre-charge resistor here?
Sometimes I've seen that a connection is bridged by hand - temporarily - for a few seconds with a power resistor and only afterwards the actual cable is connected.
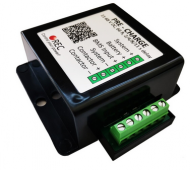
The explanation was, for example: When a device, like an inverter, is instantly connected to the battery, it is like a short circuit for the battery, which then supplies 100+ amps and kills the inverter. Because the capacitors suck themselves full and can't cope with it.
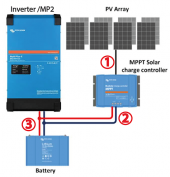
[edit] I forgot to mention: I intend to use a DIY LiFePO4 battery with 48 V and 14 kWh.
Question: Is such a pre-charge resistor really necessary or is this more like an urban myth?
(1) from the panels to the MPPT, I don't think so, a normal circuit breaker should suffice, right?
(2) at the connection MPPT <-> battery: do you need a pre-charge resistor here?
(3) at the connection battery <-> inverter: do you need a pre-charge resistor here?
Last edited: