I’m new to this forum but have been running Dacian’s SBMS in my RV for 3 + years.
So my SBMS40 has sat in a box for over a year awaiting progress on the project I intended for it. Which is finally moving ahead and taking shape. But I'm a few models behind the rest of y'all.
Maybe someone can help with some questions (I feel I've annoyed Dacian enough with my endless emails):
1) Has anyone figured out a way to rig up a remote wired display? I know you can do the whole wifi AP and web page thing on a phone. I'd prefer something simpler, wired, that doesn't require a phone. MT50, RasPi, Arduino, whatever.
I wanted this at one point but the system is so solid I only check the SOC every couple days when we’re on the road and never think about it otherwise.
2) I know there's connectors for an external thermistor but I'm getting conflicting information about how it supposed to or can be used. Dacian himself is inconsistent, calling it the battery temperature in some models and then just "external temp" in others. What actionable things can the SBMS be set to do in response to the temp readings off this probe?
I have a thermocouple on one of my battery cells. It disables charging when very cold
3) Does the SBMS40 require a heatsink? He mentions it in the manual but the SMBS40 is unique from the other models as it does not have a metal backing. So if you actually attached a heatsink, you'd be trying to pull heat just off the PCB and not actual metal. Which doesn't seem like it'd work very well.
The need for a heat sink is based how much current you’re driving in AND out. Dacian has the resistance levels of each circuit in the manual. Figure out how many watts you need to dissipate to find out whether you need a heat sink.
The MOSFETs are mounted on an aluminum board and not fiberglass so dissipation is efficient.
3b) Anyone who HAS attached a heatsink to any model SBMS: you have screw holes that you could attach the heatsink with, but then there's nothing to use to attach the SBMS itself to something. Anyone come up with an ingenious solution? Best I can come up with is cutting out the back part of the mounting board to be just shy of the dimensions of the SBMS and leaving material beneath the screw holes. Then finding a heatsink that will fit within the cut-out so it protrudes off the back. Heatsink would have to be attached with thermal glue or tape since you're using the holes to attach the SBMS to the board.
I sized my heatsink for a large discharge load of about 100A and 80A (60 from alternator + 20 from solar) of charging at the same time. In reality i’ve never had more than about 25A of loads since my inverter power doesn’t pass through the SBMS-100
The 3rd post in this thread has pics of my heat sink and shows the mounting screws I used. The 2nd post is my control panel:
https://groups.google.com/forum/m/?...er#!msg/electrodacus/FUEYKk5G6E8/KNKDiwmyAAAJ
4) I'm really struggling with the inability to put proper catastrophic breakers/fuses in the proper places for this, given its limitations (unique to the models before the SBMS0, which doesn't have this problem). I totally get why the battery must not get disconnected while the 10-pin BMS connector is connected, but it still doesn't leave me with warm fuzzies from a safety standpoint of the overall system. What have others done? Put in a fuse anyway as the last-resort safety and just accept that they'll also fry their $200+ SBMS as a result if that fuse pops?
In the earlier BMSs like ours, if you disconnected the battery positive while the sun was shining on your arrays, the solar arrays would perform the electrical equivalent of water hammer in your pipes when you turn off a faucet really fast and fry one of the ICs. To get around this, I believe Dacian recommends adding a zener diode between the pos and neg wires to dump the panel’s inductance induced voltage spike. This may permit the use of a fuse, but I’m not certain.
Fusing is intended to protect wiring. I have fuses on all my loads so the only way I could over current the batt+ wire is if it shorted to ground. I have that wire secured every few inches so there isn’t much opportunity for abrasive wear on the cable insulation and I also have most of that wire run in a fabric sleeve, split loom, or both.
If the negative wire is removed, all loads will try to use the cell sensing wires for their return path and fry your SBMS.
5) I've read and re-read the posts in this thread on the topic, but I just don't feel I understand the final answer. just how does a SBMS handle voltage coming off the panels of perhaps 17-18VDC when the batteries only want about 4VD and can get damaged by more? I'm sure the issue is solved, I just don't understand how.
The LiFePO4 battery has a very low internal resistance so it’s not possible for the charge voltage to be higher than the battery voltage. The charging voltage will always sag down to the battery voltage. An exception might be if you had had a MASSIVE array and could drive 10C or 20C or more of current. Since you have a SBMS-40, you don’t have enough power to worry about this.
6) I have some ideas on how one might use EXTIO5 and IO6 to trigger external LEDs for say "100% SOC" and "0% SOC" but I can't actually test this until some time in the future. Has anyone done something similar with any model SBMS?
You can’t have a 0% SOC LED because there would be no current to drive it. Try 20% instead.

.
When charging from my alternator I don’t like how the early SBMSs turn the charging on and off several times per minute to keep the battery topped off. The 60A battery to battery load slams my alternator too often for my comfort so I designed a latching circuit to take both these outputs and turn the alternator on at <70% charge and off again at >95% charge.
If you’re going to drive LEDs directly, and not isolated, you will be limited to 20mA so you may need to add a resistor in-line with your LED.
Edit to clean up Bb code and add pics:
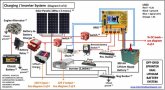
Since that schematic was finished I added an additional switch and a Bogart charge controller(minus the trimetric) to charge the chassis battery from the solar when boondocking for extended periods.