Yes, those are the specs I quoted to you. Nonsensical. Why are you using Vmp? Voc applies. Not a single panel referenced has a Voc less than 21.6V.
It's very possible to not understand something and draw wrong conclusions for decades. You're claiming that with nominal voltage panels corresponding to batteries, there is ZERO benefit of a MPPT vs. PWM. PWM have an inherent 20-30% penalty due to forced operation at battery voltage. Your claim is if you put those same "12V" panels on an MPPT, there will be no benefit over PWM. That's just absurd.
LOL- nice strawmen you like knocking down- shame literally not one of your 'arguments' has anything to do with anything I actually said...
What do you think Voltage Open Circuit means???
(hint- the open circuit bit has something to do with it)
And no- I never claimed that MPPT has no inherent value over PWM- in fact that is the exact opposite... (look at that straw fly!!!)
However an MPPT will not make any more than a PWM until it gets a high enough voltage to start operating in its MPPT mode- until then, they are running in basically PWM mode... and as your array is connected and loading the panels in PWM mode- the Voc has literally nothing to do with any of this...
And (one of the few things you got right) the panels will load down to the lowest level (17.9v for the 35w panels) and the MPPT circuitry on a Victron 100/50 doesn't start operating until it hits 5v above the battery voltage- well we got a problem don't we...
Especially as the voltage curve on a panel means it won't get anywhere near it until well into the day...
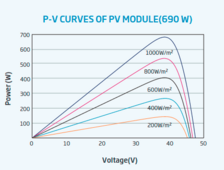
These are from a different panel (I just had these handy lol)- the voltage scale would be with the knee at 17.9v, and the Voc at 21.6v, but they all exhibit pretty much the same shape voltage curves- with the knee at 17.9v, the panels voltage is well under the minimum needed to start (not run, start) the MPPT circuitry, and as I repeatedly said- it may not even get into MPPT mode at all, if it does, it will be late in the morning if it manages at all... until then it is running as a 'very expensive PWM' controller...
Where the two in series system will only have reach half that voltage for each panel before the (superior output) MPPT circuitry kicks into life (and if you had more in series, the earlier that happens in the day, which increases the daily total power generation over the low voltage MPPT or PWM systems- which is why the high voltage systems are superior...
If you had four in series (thats getting dangerously high for the 100/50, with its extremely low PVmax rating, due to the age of its design) each panel would only have to get to 1/4 of that 'around 18v' needed, a mere 4.5v approximately per panel before the MPPT circuitry starts up and you get that 30% improvement...
(mind you, the parallel array while it is sitting at only 4.5v or there abouts, can't put a single nanoamp of charge into the battery as it has to be above the battery voltage to be able to charge at all (4.5v doesn't charge a '12v nominal' battery very well for some reason lol) and yet the high voltage MPPT is already sucking every milliwatt of power it can from that array and putting it into the battery bank...)