mrdavvv
Solar Enthusiast
- Joined
- Jan 14, 2020
- Messages
- 404
So im doing some testing in my system with the newly arrived 280AH LifePO4:

And this are my test numbers:
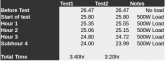
As you can see, i'm getting 3 and a half hours with a 500W load, so around 1750Whr, and considering the 50W that the inverter takes and some losses from efficiency and cabling its probably near 2000W.... But i think i should be getting at least somewhere around 4000Whr?.
This are my inverter configurations (Based on this video from will
):
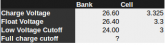
----------------------------------------------
Question 1.
What are the recommended numbers for charging / discharging?. In Will's site i found this other config:

I think this is for 10 - 90% State of charge?, maybe i should bottom balance and better use this setup?.
----------------------------------------------
Question 2.
Maybe im not completely charging the batteries?, The inverter has this option:

I placed it at FULL, but you can also setup an specific voltage. I notice that i get full charging at the beginning (40A), and then after some hours it keeps getting low, until i have around 4 -8A and after its charged it goes to float voltage at 24@1A
----------------------------------------------
Question 3.
What happens with the floating voltage?. Its my understanding that once the battery is charged, you dont need to introduce more voltage. And after "Fully" charging the battery i can see that the charger its injecting to the battery 1A@24V permanently, its this the recommended config and behavior?
----------------------------------------------
Question 4.
Overall, are my numbers good, or what i could be doing wrong?.

And this are my test numbers:
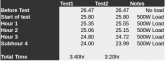
As you can see, i'm getting 3 and a half hours with a 500W load, so around 1750Whr, and considering the 50W that the inverter takes and some losses from efficiency and cabling its probably near 2000W.... But i think i should be getting at least somewhere around 4000Whr?.
- 24V @280Ah = 6720W
- Charge / Discharge Profile 20 to 80%
- So using 60% of full capacity = 4000W
This are my inverter configurations (Based on this video from will
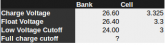
----------------------------------------------
Question 1.
What are the recommended numbers for charging / discharging?. In Will's site i found this other config:


All-in-One Solar Power Packages
MPP and a few other manufacturers now sell a "complete off grid system in a box" that has: AC Inverter Solar Charge Controller AC Battery Charger Automatic Transfer Switch (if grid power is...
www.mobile-solarpower.com
I think this is for 10 - 90% State of charge?, maybe i should bottom balance and better use this setup?.
----------------------------------------------
Question 2.
Maybe im not completely charging the batteries?, The inverter has this option:

I placed it at FULL, but you can also setup an specific voltage. I notice that i get full charging at the beginning (40A), and then after some hours it keeps getting low, until i have around 4 -8A and after its charged it goes to float voltage at 24@1A
----------------------------------------------
Question 3.
What happens with the floating voltage?. Its my understanding that once the battery is charged, you dont need to introduce more voltage. And after "Fully" charging the battery i can see that the charger its injecting to the battery 1A@24V permanently, its this the recommended config and behavior?
----------------------------------------------
Question 4.
Overall, are my numbers good, or what i could be doing wrong?.