Jusst set to manual voltage?
You can have Deye use Batt V.
However LifePo4 voltage changes when charging/discharging/resting making Time Of Use not be reliable.
I mean, take a look at this Time Of Use (in voltages) example from Deye manual:
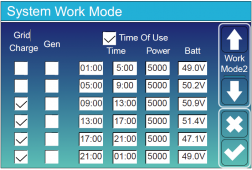
First line 01:00-05:00, Deye will stop inverting (supply power) when Battery dips below 49.0V.
But after a few minutes, battery will recover a few millivolts and be >49V again.
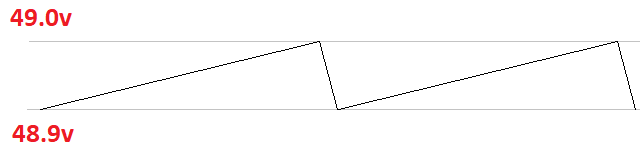
Deye will start inverting again and then drops down. rinse repeat with longer gaps.
Time Of Use does not have Hysteresis to prevent this situation.
This is where using Batt % is advantageous with Time Of Use.
From my observation with Deye:
1. Deye keeps track of your Battery's SOC internally by adding SOC% when charging, and deducting SOC% when discharging.
2. Unfortuantely Deye suck at keeping track of small flow, this drifts ~1% per day.
3. This internal count resets when battery disconnects: Resets to 0% when UVP and resets to 100% when OVP. This means, if you can fully charge your batteries at least once a week, you can be assured Deye's SOC% count will be fairly accurate for the week.
One method to guarantee full charge battery (once a week) is using Time Of Use: Set one day to conserve battery (set all Battery levels to 100%), allowing the next day to fully charge batteries..
But if you are already using Time Of Use for other stuff, then this method is a no go.