buryck
New Member
- Joined
- Mar 31, 2020
- Messages
- 22
I made the updated schematic which includes the BMS and the Victron Smart Shunt (500A)
The Smart shunt will connect to the CCGX of the EasySolar along with the smaller MPPT through the VE.Direct ports. And since the reading from the Smart shunt will be the main voltage reading source which all other Victron components will use, i can set the charge upper limit to 80% and the discharge lower limit to 20%. That will prevent the BMS from even getting close to trigger a disconnect. It will be there just in case something goes bad with my settings and to ballance the cells. I think i can get by with only using 60% of the battery capacity, maybe 70% if i push the SoC to 90%.
What do you guys think?
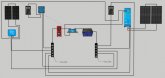
*ballance cables not connected in the diagram, they will be connected in real life.
The Smart shunt will connect to the CCGX of the EasySolar along with the smaller MPPT through the VE.Direct ports. And since the reading from the Smart shunt will be the main voltage reading source which all other Victron components will use, i can set the charge upper limit to 80% and the discharge lower limit to 20%. That will prevent the BMS from even getting close to trigger a disconnect. It will be there just in case something goes bad with my settings and to ballance the cells. I think i can get by with only using 60% of the battery capacity, maybe 70% if i push the SoC to 90%.
What do you guys think?
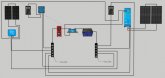
*ballance cables not connected in the diagram, they will be connected in real life.