I was shocked(astonished ?) by the looseness of a number of my cell terminal nuts even though I had re-torque them days after the original assembly. Three different 16s batteries but two had similarities and similar issues. None of the batteries had any electrical issues(yet), beautiful balance and performance, I just now simply checked out of a whim and curiosity six months later. The two problematic batteries have cells are the CATL 302 Ah welded terminals type that have the small contact diameter on top. The last battery that’s only been in service a few months is an EVE LF280K double hole post with flexible buss and exhibited very very slight nut loosening and of those it was only the ones with balance eye terminals and the positive and negative Selterm cable lugs. The CATL cell were from two different sources with two different types of welded terminals. One with taller posts and no stud and one with stud. The taller posts allowed me to use a longer grub screw that facilitated the use of a Belleville washer and flat washer beneath it but of course above the conductor. On all batteries the nuts used are flat smooth bottom, not the common serrated concave, balance lead eye terminals are plated hard brass, not soft copper. During assembly the oxides were removed from from both contact surfaces without compromising flatness or plating, “NO-OX ID A special” applied to contact surfaces while avoiding the threads and nuts torqued to 4Nm.
My realizations: #1 Stainless Belleville washers( two different brands) are useless as these were the loosest. These flatten out well before full torque and do not recover in shape after being used especially with time. #2 And most importantly to understand is, copper busses, lugs or jumpers will flow when there is a confined point of contact (small terminal area) and this yielded space must be taken up until it subsides as needed. The metal will flow the most initially. #3 The large mounting surface LF280K with a flexible buss(resistance welded ends) tho the youngest, seemed to be more solid in terms of torque, so far and will factor greatly in any future purchases.
If you haven’t checked lately, perhaps you should. Please report back on your results, experiences and thoughts.
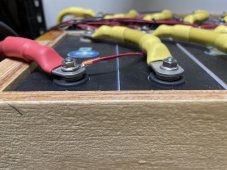
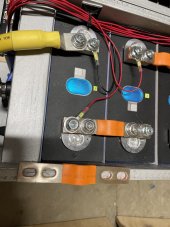
My realizations: #1 Stainless Belleville washers( two different brands) are useless as these were the loosest. These flatten out well before full torque and do not recover in shape after being used especially with time. #2 And most importantly to understand is, copper busses, lugs or jumpers will flow when there is a confined point of contact (small terminal area) and this yielded space must be taken up until it subsides as needed. The metal will flow the most initially. #3 The large mounting surface LF280K with a flexible buss(resistance welded ends) tho the youngest, seemed to be more solid in terms of torque, so far and will factor greatly in any future purchases.
If you haven’t checked lately, perhaps you should. Please report back on your results, experiences and thoughts.

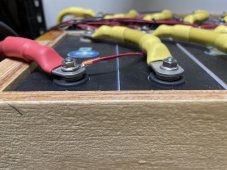
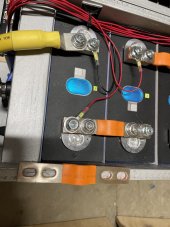
Last edited: