cringely
New Member
- Joined
- Oct 25, 2019
- Messages
- 7
I have a homebuilt airplane, a Thorp T-18C, which carries two people and has a Lycoming IO-320-B1A engine rated at 160 hp. I'll shortly be getting it back in the air following a six-year rebuild (the plane was originally built in 1999). It needs a new 12V battery (for starting, radios, etc., just like a car) and I am thinking of building my own.
Here is the plane:
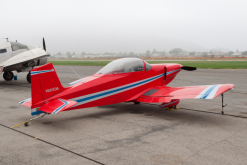
Here is the battery I'm replacing: http://concordebattery.com/flyerprint.php?id=35
It's 12V, 22 amp-hours, 225 CCA, and 22.7 lbs (ouch!). Oh, and because it's for airplanes it costs $260.
There are now lithium batteries available for this application. They crank better and weigh a LOT less (7 lbs compared to 22), but are even more expensive at $609: https://www.aircraftspruce.com/catalog/elpages/earthxbatteries_11-16211.php
Since this is an experimental amateur-built aircraft there really is no rule against my building my own battery, so I am starting (if this is wrong, please tell me) with four of these cells from Battery Hookup: HEADWAY 38120 HP 3.2V 8AH LIFEPO4 BATTERY. They are now sold out but my four cells arrived today.
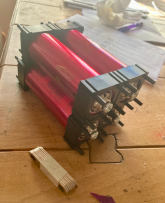
There is a BMS available, which I didn't buy but can still order one.
The whole package is about three lbs.
Now I have to decide how to build the actual battery. It will be mounted on the firewall right by the engine, replacing the former battery, so the cable lengths are all short. I doubt that I will EVER charge this battery at below-freezing temps. I wouldn't start the engine below freezing for one thing (pre-heat -- airplane engines are pampered), and it won't charge without the engine running. I can build it 2X2 or as a 1X4 flatpack, which might mount better on the firewall. Oh, and Will, the plane is in LAS VEGAS.
Here is the plane:
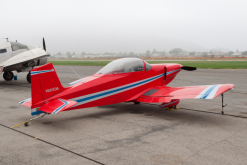
Here is the battery I'm replacing: http://concordebattery.com/flyerprint.php?id=35
It's 12V, 22 amp-hours, 225 CCA, and 22.7 lbs (ouch!). Oh, and because it's for airplanes it costs $260.
There are now lithium batteries available for this application. They crank better and weigh a LOT less (7 lbs compared to 22), but are even more expensive at $609: https://www.aircraftspruce.com/catalog/elpages/earthxbatteries_11-16211.php
Since this is an experimental amateur-built aircraft there really is no rule against my building my own battery, so I am starting (if this is wrong, please tell me) with four of these cells from Battery Hookup: HEADWAY 38120 HP 3.2V 8AH LIFEPO4 BATTERY. They are now sold out but my four cells arrived today.
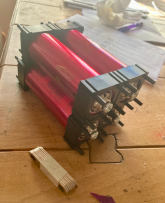
There is a BMS available, which I didn't buy but can still order one.
The whole package is about three lbs.
Now I have to decide how to build the actual battery. It will be mounted on the firewall right by the engine, replacing the former battery, so the cable lengths are all short. I doubt that I will EVER charge this battery at below-freezing temps. I wouldn't start the engine below freezing for one thing (pre-heat -- airplane engines are pampered), and it won't charge without the engine running. I can build it 2X2 or as a 1X4 flatpack, which might mount better on the firewall. Oh, and Will, the plane is in LAS VEGAS.