I'm hoping this post starts a discussion, I'm not judging. Let me know if you want a new thread started instead.
Nope, lets discuss!
I have no issue with judgement and no shame. Im always open to any criticism so please feel free to not filter an opinion.
“If you are not willing to be a fool, you can't become a master.”
Jordan b. Peterson
I'm getting ready to put in some copper flat bar, similar to how you're doing. I thought about buying 1" wide flat bar. However, I got to thinking that if the surface contact area is no bigger than 3/4" flat bar would cover, is there any sense in going to 1". Sure 1" flat bar has a bigger cross section and can handle more amps. But if the surface contact area is so much smaller, have I wasted 1/4" of flat bar?
I bought the copper bar based on the surface of the shunt (1.5" wide) and because it would fit everywhere else. The only exception is the bar coming out the top of the switch on the right. It is 2" wide because the out for the switch is like in the picture below but the output (two of them) is where input 1 and input 2 are and the input is where the output is. The 2" bar made it so I could connect to both posts and I cut out the side of the switch housing to let the bar exit the side. It just make it nicer to do.
As Hedges said above, the bigger bar also helps with cooling so it would pull some heat away from the shunt
Not having as much knowledge in this arena as I would like I have simply been trying to err on the side of overkill. You waste a little money but you dont lose it all.
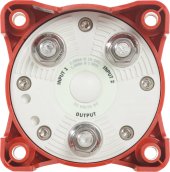