Pieter Blackie
New Member
Hi All, I am a long time reader but first time poster, I have been following Will for a while now and have watched every video on the channel
this is a summary of the system I have just completed
24v 3KVA Solar Inverter Charger Hybrid Pure Sine Wave PWM 50A Regulator PV 80VAC AU
2x 12V 350W Solar Panel Mono
2 x Rapid X 12V 100Ah Lithium Ion Battery LiFePO4
150A Digital LCD Watt Meter Power Analyser
I do however have a problem
My batteries takes forever to charge off solar and even connecting to mains it still takes forever
seems as if the charge to battery is limited and it looks as if the batteries BMS is the cause but how do I test this
Also does not look as if If my batteries in series want to charge higher that 27v
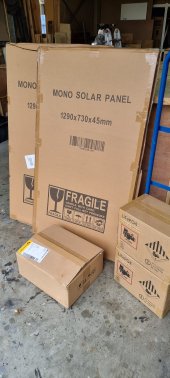
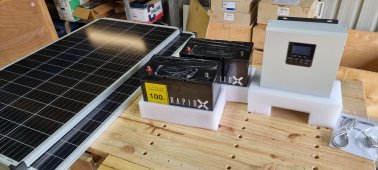
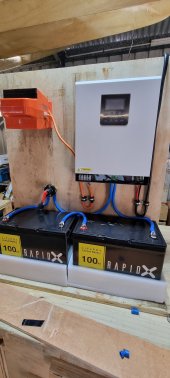
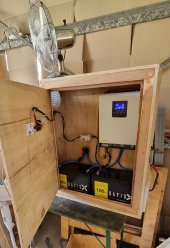
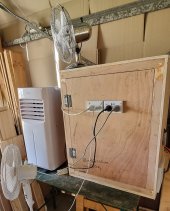

this is a summary of the system I have just completed
24v 3KVA Solar Inverter Charger Hybrid Pure Sine Wave PWM 50A Regulator PV 80VAC AU
2x 12V 350W Solar Panel Mono
2 x Rapid X 12V 100Ah Lithium Ion Battery LiFePO4
150A Digital LCD Watt Meter Power Analyser
I do however have a problem
My batteries takes forever to charge off solar and even connecting to mains it still takes forever
seems as if the charge to battery is limited and it looks as if the batteries BMS is the cause but how do I test this
Also does not look as if If my batteries in series want to charge higher that 27v
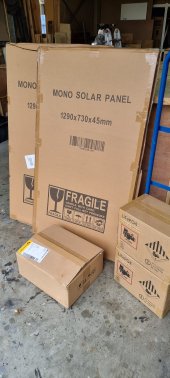
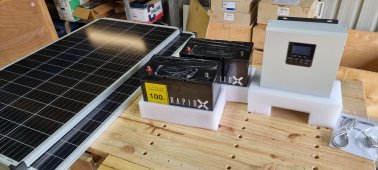
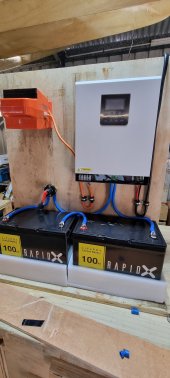
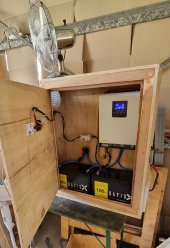
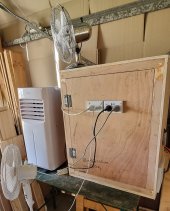
