idontknowwhatimdoing
New Member
- Joined
- Jul 6, 2020
- Messages
- 105
Hey crew,
Currently have the standard configuration of 4s 280ah & I want to change it to a "slim" configuration.
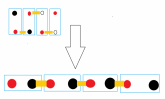
This install is four my four wheel drive and in the current configuration it takes too much space up unnecessarily.
Now, the trade off for this configuration is the mechanical integrity of the battery. So I believe flexible BUSBARS would be a much safer option. Would this braid be sufficient? and I'll just use tinned copper pipe for the lugs, pressed on the braid. https://tinyurl.com/y2alnuxq.
To give strength to the longest side of the battery to provide adequate compression for optimum battery health, I will 3D print INDIVIDUAL cell casings, which will slide into a plywood box.
Are there any flaws in this, or advice?
Thanks in advance!
Currently have the standard configuration of 4s 280ah & I want to change it to a "slim" configuration.
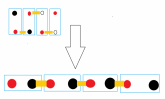
This install is four my four wheel drive and in the current configuration it takes too much space up unnecessarily.
Now, the trade off for this configuration is the mechanical integrity of the battery. So I believe flexible BUSBARS would be a much safer option. Would this braid be sufficient? and I'll just use tinned copper pipe for the lugs, pressed on the braid. https://tinyurl.com/y2alnuxq.
To give strength to the longest side of the battery to provide adequate compression for optimum battery health, I will 3D print INDIVIDUAL cell casings, which will slide into a plywood box.
Are there any flaws in this, or advice?
Thanks in advance!