I've been doing a deep dive into my pylontech battery (three US5000 connected in parallel to a solis RHI-6K-48ES-5G-DC hybrid inverter). I had always assumed that the pylontech battery would communicate the correct charge voltage settings to the inverter through the CAN bus. But I am now not sure this is the case. Before I start playing with my inverter settings I am seeking some feedback to see if anyone else has gone down this rabbit hole ! 
On the inverter under Advanced Settings : Storage Energy Set : Control Parameters is the following screen
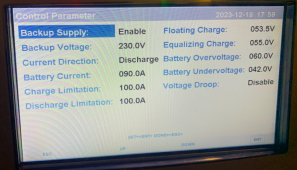
First observation is that the Battery Overvoltage and Undervoltage look well wrong.
Pylontech running 15 cells with a max voltage of 3.6v per cell should make the overvoltage = 54v, certainly not 60V ! and the pylontech manual says that the battery min voltage should be 44.5v
Probably not of a huge concern as the battery BMS will kick in its own protection if the correct values are exceeded, but just surprised these are wrong in the inverter. Clearly the CAN bus is not setting them!
More interestingly I have connected to the RS485 port on the master US5000 battery to log the cell voltages during a typical charge cycle to 100% and see the following

I have ~80mV imbalance across all the cells in each of the three battery packs which isn't bad, but the Solis inverter doesn't appear to be entering a float voltage state of 53.5v for any period of time to allow the BMS to balance the packs ????? I can only guess that the float voltage of 53.5v (3.56v/cell) is very close to the likely 3.6v cell limit in the pylontech BMS. Some cells seem to be very close to 3.6v which could then be triggering a charge shutdown to the inverter through the CAN bus and cutting short any float mode. This indicates to me that the float voltage is set too high and needs to be reduced to at least 53v if not 52.5v to allow the BMS balancer to have time to balance the pack (and with only a reported 50mA balancer in the pylontech BMS this needs a good few hours !)
Charge shut-down and over voltage protection is not reported through RS485 and I haven't got a CAN bus reader to verify this hypothesis (one is on order !). But I had expected that the pylon battery to control the charge voltage through the CAN link but this doesn't appear to be the case, unless this is the expected operation but it doesn't look right to me. Seems that the battery could get out of balance over prolonged use with these settings.
Before I start playing with the inverter parameters has anyone got any detailed experience of the pylontech/solis charge/balancing cycle ?
Are these the results I should be expecting ?
Thanks in advance
On the inverter under Advanced Settings : Storage Energy Set : Control Parameters is the following screen
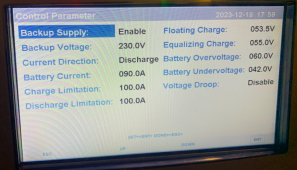
First observation is that the Battery Overvoltage and Undervoltage look well wrong.
Pylontech running 15 cells with a max voltage of 3.6v per cell should make the overvoltage = 54v, certainly not 60V ! and the pylontech manual says that the battery min voltage should be 44.5v
Probably not of a huge concern as the battery BMS will kick in its own protection if the correct values are exceeded, but just surprised these are wrong in the inverter. Clearly the CAN bus is not setting them!
More interestingly I have connected to the RS485 port on the master US5000 battery to log the cell voltages during a typical charge cycle to 100% and see the following

I have ~80mV imbalance across all the cells in each of the three battery packs which isn't bad, but the Solis inverter doesn't appear to be entering a float voltage state of 53.5v for any period of time to allow the BMS to balance the packs ????? I can only guess that the float voltage of 53.5v (3.56v/cell) is very close to the likely 3.6v cell limit in the pylontech BMS. Some cells seem to be very close to 3.6v which could then be triggering a charge shutdown to the inverter through the CAN bus and cutting short any float mode. This indicates to me that the float voltage is set too high and needs to be reduced to at least 53v if not 52.5v to allow the BMS balancer to have time to balance the pack (and with only a reported 50mA balancer in the pylontech BMS this needs a good few hours !)
Charge shut-down and over voltage protection is not reported through RS485 and I haven't got a CAN bus reader to verify this hypothesis (one is on order !). But I had expected that the pylon battery to control the charge voltage through the CAN link but this doesn't appear to be the case, unless this is the expected operation but it doesn't look right to me. Seems that the battery could get out of balance over prolonged use with these settings.
Before I start playing with the inverter parameters has anyone got any detailed experience of the pylontech/solis charge/balancing cycle ?
Are these the results I should be expecting ?
Thanks in advance
Last edited: