Frank in Thailand
making mistakes so you don't have to...
Hi all,
During my green LiFePO4 day's I used the screws provided by the sellers, and changed the setup a few times.
Needless to say that the threads in the weak aluminium didn't like that.
Git got that far that about half of the 48x 152 terminals are out of tread, locking agent no longer helps, wd-weld or similar.. can't hold +4 Nm torque
So I have the nice task of fixing 96 holes.
I have 17/64 - 6.75mm drill and thread set.
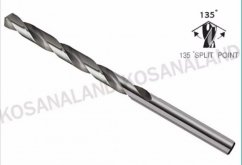
The drill I grinded most of the tip flat, the 6mm is already there, it's just 0.75mm
The taps is a quality set:
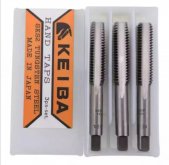
I used my standing drill without motor (took of the belt and turned by hand)
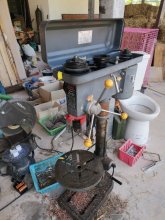
Pics say more then words, here is the progress:
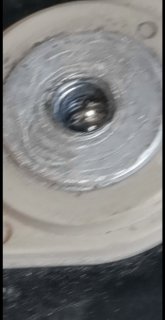
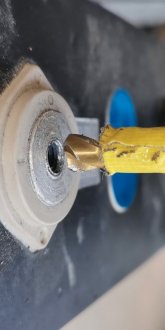

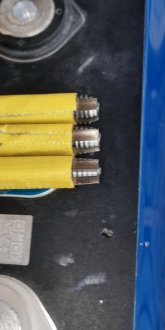
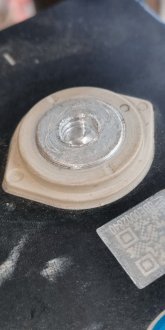
During my green LiFePO4 day's I used the screws provided by the sellers, and changed the setup a few times.
Needless to say that the threads in the weak aluminium didn't like that.
Git got that far that about half of the 48x 152 terminals are out of tread, locking agent no longer helps, wd-weld or similar.. can't hold +4 Nm torque
So I have the nice task of fixing 96 holes.
I have 17/64 - 6.75mm drill and thread set.
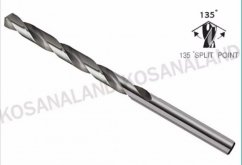
The drill I grinded most of the tip flat, the 6mm is already there, it's just 0.75mm
The taps is a quality set:
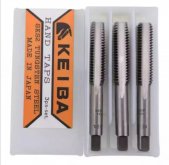
I used my standing drill without motor (took of the belt and turned by hand)
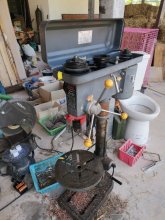
Pics say more then words, here is the progress:
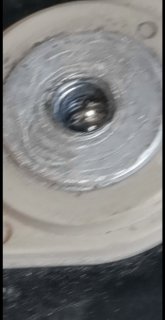
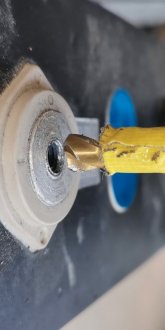

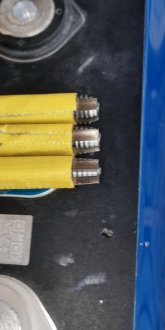
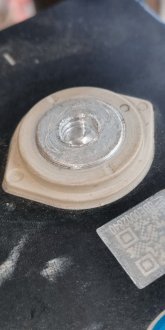