OK, so I bought the Poron 50-15250 sheet from McMaster.
I used the chart provided by the manufacturer to estimate the compression for my 4S battery. I have cut most of the parts for the frame but have not put it together yet because I have not drilled all the screw holes. This battery will have one sheet of foam compressed roughly 15%, which should yield about 9 PSI. One 1/4" sheet should also allow for 0.5mm (~0.020") expansion of each cell, for a total of 0.080" expansion and a pressure just under the magic 18 PSI maximum specified by EVE. Here is the manufacturer's chart:
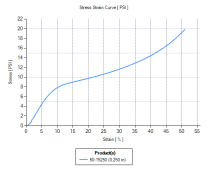
This should work well, depending on the long-term performance of the foam, but the more pressing question is what will I do for the two 16S batteries I am also making? One sheet of foam is not enough to allow for that much expansion, but two sheets will cover eight cells, and I can build boxes of eight and get my two 16S batteries that way. The question now is, what happens when I use two sheets of foam in one stack?
Rather than blindly trust the chart above and make a curve assuming they will behave as parallel springs, I decided to measure the stuff. It isn't a true linear spring after all, and I figured out how to do it with a few things I have lying around (such as a kitchen scale and a CNC mill). Here we go!
First, I had to measure the force shown on the scale at different displacements since the pan moves down slightly as you press on it. I put the scale on the mill bed, added a small (about 4" square) piece of 1/8" masonite to distribute the force on the pan, and proceeded to press down on the scale with a 1.25" diameter cylinder. I recorded the scale readings every 0.001" from 0" to 0.046", where the scale was near its upper limit.
I then made a spreadsheet with the recorded values and fit a seventh-order polynomial to the data, which gives me a displacement adjustment per force measured so I can calculate the actual amount the foam displaced under that load. Here is the adjustment curve (X is grams, Y is inches):
I cut two pieces of foam. The goal was exactly one square inch each, but the foam is just a bit pesky to cut, so I wound up with one at 1.035 and the other 1.045 square inches. The final adjusted force measurements are normalized by these values to give pounds per square inch. I measured the first square of foam by placing it on the scale and topping it with a 1.25" square piece of 1/16" plastic to distribute the force on the foam. After zeroing the scale, I proceeded to press the foam in 0.010" increments from 0" to 0.200", where the scale was close enough to its maximum value (and the foam was compressed 80%). I then replaced the foam with piece number two and repeated the experiment.
Finally, I made a Poron sandwich with foam, plastic, foam, and plastic on the scale and pressed that stack from 0" to 0.360", where the scale was near its maximum. All of this measuring was very slow going since I had to wait about a minute at each step to let the foam stabilize. It was easy to see that it was losing quite a bit of the initial force after changing the displacement, so I had to let it settle a bit. I could not wait for it to stop completely because the scale would go to sleep. It was also 97°F (35°C) in my shop today with the doors open, so I was OK with watching the force slow down and making an estimate after one minute. I then made a spreadsheet with the data.
I used the scale adjustment curve to subtract the scale displacement from my recorded displacement values so that I now have foam displacement only. I used the area adjustments for both pieces to normalize the force measurements to PSI. But enough of all that, here's the result:

So, it seems that a stack of eight cells with two sheets of foam can expand up to 8X0.5mm = 4mm (~0.160") and still be below 18 PSI if I start with a 0.2" total (0.1" per sheet) displacement in the foam. That should give me a range of about 7.5 to 18 PSI over the expected expansion of the cells. It also seems that my 4S battery will start at about 5 PSI, not 9 PSI. Oh, well.
Enjoy!