Hi all, I found a bargain ebay purchase and trying to make an ESS for self consumption.
I have a background in IT and some engineering, but admit I'm a complete noobie. This is new to me and I want to be safe. Here's the proposed setup:
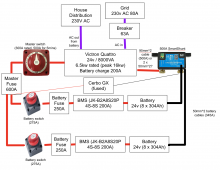
I have a Victron Quattro 24v 8000VA (6500w rated) inverter (datasheet of specs attached). My energy provider offers cheap tariffs at 1/3 of the day rate price (so its 12p per kwh from 11pm to 5pm). I want to charge batteries at night then use through the day. I've seen some 304Ah batteries on sale (datasheet attached). I only have the inverter right now and have been researching for past few weeks but confused here and there. Not sure if I've spec'd out a safe and reliable system that will meet my needs. Any help would be appreciated
My thoughts - am I on the right track?:
I've probably made some errors in here and missed some things out. Please be patient with me
I have a background in IT and some engineering, but admit I'm a complete noobie. This is new to me and I want to be safe. Here's the proposed setup:
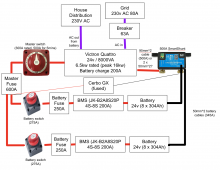
I have a Victron Quattro 24v 8000VA (6500w rated) inverter (datasheet of specs attached). My energy provider offers cheap tariffs at 1/3 of the day rate price (so its 12p per kwh from 11pm to 5pm). I want to charge batteries at night then use through the day. I've seen some 304Ah batteries on sale (datasheet attached). I only have the inverter right now and have been researching for past few weeks but confused here and there. Not sure if I've spec'd out a safe and reliable system that will meet my needs. Any help would be appreciated
My thoughts - am I on the right track?:
- Overall ESS Setup Summary:
- 8s2p battery bank consistes of two packs of cells, connected via 50mm^2 battery cables cut same length
- Each battery pack fused with class T/ANL fuse of around 250A
- JK 4s-8s 200A BMS on each battery pack.
- Victron 500A smartshunt added to negative terminal of inverter and all battery pack negatives connected directly to that
- Main DC system fuse of 600A
- Capacity:
- 12kwh daily use => 304Ah battery capacity x 16 cells x 3.2v = 15.5kwh capacity => about 3kwh spare so i drain to 20% SOC everyday to keep battery healthy.
- Battery packs:
- Each battery pack would be 8 in series so its two packs in parallel e.g. 8s2p. This would give 24v and 608A max (currents add up but voltage stays same).
- Current draw:
- Inverter can run continuously at 6500w => 6500 / 24 = 270A total rated current draw. If I keep battery leads the same length, can I assume its (270/2) = 135A that will be drawn from each battery pack?
- BMS:
- Victron inverter has protection capabilities but from watching off grid garage and will, etc it seems better to have a BMS. Not sure if it needs to be active or passive but JK BMS seems right way to go (maybe Daly or passive thing like Helltec). To be safe I'm leaning on the idea of a JK BMS (JK-B2A8S20P 4S-8S 200A) on each battery pack.
- From off grid garage channel I've gleaned to bulk charge upto 3.45v then it should go into absorption for half hour or so after that as not to overcharge (eg charge quickly to 80% then let it trickle charge up the rest of the way).
- A part of me thinks I only need a passive balancer as its cheaper and only needs to top balance the battery cells when its over 3.45v - thoughts?
- Charging:
- Factors and assumptions:
- 15.5kwh capacity,
- Victron 24v battery charger with 200A capability
- 230v mains (with 80A grid connection fuse)
- JK BMS with 200A cutoff
- 6hours of off-peak electricity
- Victron limit charging to 75% of rated power => 6500w x 75% = 4875w => 4875w / 24v = 203A (in specs it says 200A)
- If the factors and assumptions are correct (assuming battery fully depleted) so 15500 wh / 4875w = just over 3 hours to replenish batteries at full charge.
- Another factor is what is a healthy charge rate of the 304Ah batteries? On the spec sheet (see attached - who knows if its credible) it says they are tested at 150A charge and discharge rates. On off grid garage channel, he charges and discharges (i think) around 40A. Not sure what is healthy, safe and realistic charge rate should be here?
- Factors and assumptions:
- Protection:
- Inverter can peak at 16kw and continuous at 6.5kw. I'll run just under the continuous rating but due to electrical surges in appliances and motors etc (washing machines, electronics, etc switching on) I'm guessing I should fuse for peak so 16000w / 24v = 667A. Would a 600A fuse suffice to act as main fuse on positive entry to inverter to cut everything off and cables burn?
- Lynx distributor seems to be neat and use mega fuses - do I need it in my setup? I was thinking i connect directly to terminals on switch or shunt. In future I do want to add an MPPT but maybe only one.
- The JK BMS appears to cut off at 200A, 50mm^2 battery/welding wire is rated at 345A, battery pack current draw is 135A per pack (if parallel working assumptions are correct from #3) => 250A ANL fuse for each battery pack should suffice?
- Alternatively I can use DC solar breakers that are 250A but are high DC voltage - will they work for battery protection better to stick to switch and fuse combo?
- On a youtube forum it was recommended by 'TTSmith' that Schneider INS250 should be used to prevent DC arc'ing and welding.
- Most people say to use class T fuses as the main fuse but the Victron lynx shunt itself uses cheaper ANL fuse. I'm confused if there's really a benefit for home ESS to use more expensive class T. I'm not using a Lynx shunt (they're so expensive but grudgingly will use class T - any concise thoughts? (I know that is a huge topic).
- Monitoring:
- I have an old tablet that will be mounted alongside the setup to connect to VRM
- JK BMS can be bought with small LCD screens not sure if I need this as I can bluetooth in from the tablet
I've probably made some errors in here and missed some things out. Please be patient with me
Attachments
Last edited: