TerryTtibbs
New Member
- Joined
- Mar 15, 2022
- Messages
- 56
Calling all Copper Lug Guru's - which lug would you choose and why?
I have ordered from 2 suppliers. 1 is an electrical supplier and the other specialise in DC cable and Forklifts, HGV and all the big Automotive stuff.
The shorter lugs on the left are from the DC cable and big stuff guys and are the more expensive by 20%, they also have a smaller inspection window, both weigh 8g.
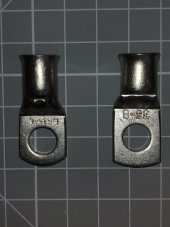
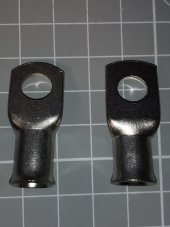
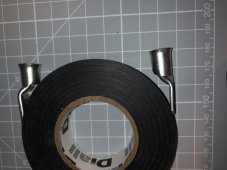
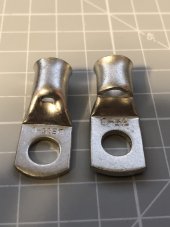
Opinions please.
I have ordered from 2 suppliers. 1 is an electrical supplier and the other specialise in DC cable and Forklifts, HGV and all the big Automotive stuff.
The shorter lugs on the left are from the DC cable and big stuff guys and are the more expensive by 20%, they also have a smaller inspection window, both weigh 8g.
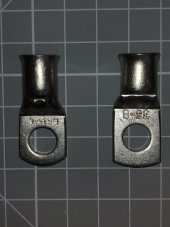
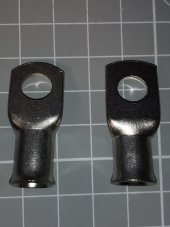
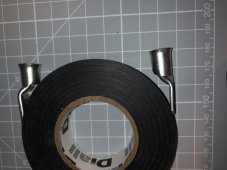
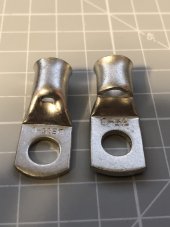
Opinions please.
Last edited: