Steve_S
Offgrid Cabineer, N.E. Ontario, Canada
Good Day Folks !
Note:
I have no affiliation with Chargery whatsoever, I'm just a customer sharing info in the best interest to help others.
I purchased a Chargery BMS8T a month or so ago as a replacement BMS for my ShunBin pack. Post showing installation on ShunBin Pack The installation has been pretty straight forward but one feature the BMS did not have was a Low Temp cutoff. After some discussions with Jason Wang @ Chargery, new firmware has been made... Chargery BMS / Balancer page YES that's right, they can have their firmware updated, unlike most other BMS'. The Firmware can be updated on the main unit to version V1.22, & the LCD unit version to V3.03 which will now support Low Temp Cutoff.
Electrical Vehicle including E-Motorcycle, E-Scooter and so on. The unit can measure or detect the battery voltage,
cell voltage, charge & discharge current, battery temperature, and battery SOC (State of Charge) , displayed with
TFT color LCD.
New Updated Documentation Is being prepared TODAY and the firmware & docs should be posted within the next day or two. (doc's need a bit more polish).
Link to Setup Screen for Low Temp & Table of Features (post 10)
* I've also highlighted the customer desire for BlueTooth / Wifi connectivity as a good bonus to have available. They currently have an RS232 interface which a PC can access but this is not a simple and easy method that many prefer. I cannot be certain if/when such may be available but finger's crossed that they are cooking it up, possibly as an extra small module or something.. I believe if enough people ask for it, that would support having such a feature done quicker.
So far, I am quite pleased with the hardware, it all works as expected and easy enough to install & setup, albeit the manuals need clarity so take your time. I chose to use a Deltec 500A/50mv Shunt as opposed to the one supplied by them, not only because the Deltec's have a backing & can be surface mounted, they are Brass Units and calibrated for accuracy. The Heavy Duty N.O. Relays are pretty serious, so I kept those but any High End 12V relay that is rated for the AMPS will work fine if you want to go electronic vs mechanical.
The BMS8T kit as I received it (I purchased directly from Chargery and they expedited shipping and it was great ! )
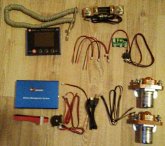
REF for Deltec Shunt:
ARE YOU SEEING RIPPLE ON THE BMS ?
Do you have EMI/RFI ISSUES ??
Are Amps In/Out or Voltages "fluttering" ???
It could be your Wiring Layout !
SEE THIS POST:
diysolarforum.com
Note:
I have no affiliation with Chargery whatsoever, I'm just a customer sharing info in the best interest to help others.
I purchased a Chargery BMS8T a month or so ago as a replacement BMS for my ShunBin pack. Post showing installation on ShunBin Pack The installation has been pretty straight forward but one feature the BMS did not have was a Low Temp cutoff. After some discussions with Jason Wang @ Chargery, new firmware has been made... Chargery BMS / Balancer page YES that's right, they can have their firmware updated, unlike most other BMS'. The Firmware can be updated on the main unit to version V1.22, & the LCD unit version to V3.03 which will now support Low Temp Cutoff.
- Low temp. cutoff in charge -20C min. 20C max.
- Low temp. cutoff in discharge -20C min. 20C max.
Electrical Vehicle including E-Motorcycle, E-Scooter and so on. The unit can measure or detect the battery voltage,
cell voltage, charge & discharge current, battery temperature, and battery SOC (State of Charge) , displayed with
TFT color LCD.
New Updated Documentation Is being prepared TODAY and the firmware & docs should be posted within the next day or two. (doc's need a bit more polish).
Link to Setup Screen for Low Temp & Table of Features (post 10)
* I've also highlighted the customer desire for BlueTooth / Wifi connectivity as a good bonus to have available. They currently have an RS232 interface which a PC can access but this is not a simple and easy method that many prefer. I cannot be certain if/when such may be available but finger's crossed that they are cooking it up, possibly as an extra small module or something.. I believe if enough people ask for it, that would support having such a feature done quicker.
So far, I am quite pleased with the hardware, it all works as expected and easy enough to install & setup, albeit the manuals need clarity so take your time. I chose to use a Deltec 500A/50mv Shunt as opposed to the one supplied by them, not only because the Deltec's have a backing & can be surface mounted, they are Brass Units and calibrated for accuracy. The Heavy Duty N.O. Relays are pretty serious, so I kept those but any High End 12V relay that is rated for the AMPS will work fine if you want to go electronic vs mechanical.
The BMS8T kit as I received it (I purchased directly from Chargery and they expedited shipping and it was great ! )
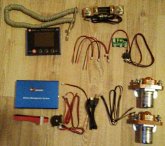
REF for Deltec Shunt:

DELTEC 500 AMP 50 MILLIVOLT CURRENT SHUNT | eBay
Deltec 500 Amp 50mV Shunt. Where mounting bases are provided, high strength phenolic is used with mounting holes designed in for ease of use. Shunts should be located in an area where freely circulating air is available.
www.ebay.com
ARE YOU SEEING RIPPLE ON THE BMS ?
Do you have EMI/RFI ISSUES ??
Are Amps In/Out or Voltages "fluttering" ???
It could be your Wiring Layout !
SEE THIS POST:

Chargery BMS now with Low Temp Cutoff
This might be a dumb question, but why not use a load-side lockout relay or some kind of disconnect that's triggered by the BMS vs having a NO power sucking relay on the Chargery? A couple of reasons that come to mind are that the power relays do use a lot of power .... and, to get a good one...

Last edited: