Very new to this. I had my PV and inverter installed last year and I'm just trying to get optimal usage out of it. My installer is not familiar with any of the advanced features if the inverter, they include it just for critical load/battery backup.
The objective is to get the inverter to *not* charge the battery from solar when there's an active household load (loads not on my critical loads transfer switch). I discharge the battery overnight so I buy less grid power, and it starts charging as soon as the sun comes up. But I *don't* want it to charge if, say, I run my AC or car charger (not on the hybrid inverter). My understanding is that this is "zero export to CT" mode. But, when I activate this mode, the readouts don't make any sense.
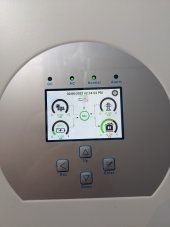
I've attached some pictures from the middle of the day with not much demand in Zero Export to CT mode. From the photos you can see it reports a 5kw load, but in reality it's probably more like 1kw. And for whatever reason it is drawing from the battery even though the 4kw of solar coming in is plenty for everything. My sense energy monitor and AP systems portal are in agreement about my solar production, but it sees the solar input as a load?
RIght now I've got the CTs installed on grid side of the main breaker. I've also tried having them installed on the grid connection at the inverter itself, which more or less produces the same behavior.
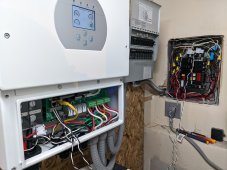
I suspect this is due to the way that things are wired connected at my MSP, but I'm not sure how to resolve it. Or maybe it's because I'm using the grid input as my solar input (manuals say this is correct, but maybe the SW doesn't like it.)
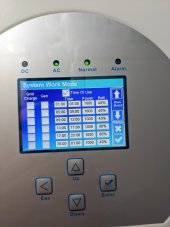
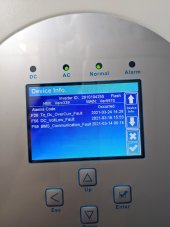
The objective is to get the inverter to *not* charge the battery from solar when there's an active household load (loads not on my critical loads transfer switch). I discharge the battery overnight so I buy less grid power, and it starts charging as soon as the sun comes up. But I *don't* want it to charge if, say, I run my AC or car charger (not on the hybrid inverter). My understanding is that this is "zero export to CT" mode. But, when I activate this mode, the readouts don't make any sense.
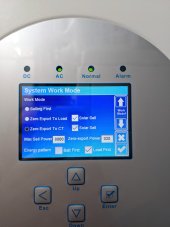
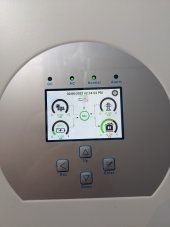
I've attached some pictures from the middle of the day with not much demand in Zero Export to CT mode. From the photos you can see it reports a 5kw load, but in reality it's probably more like 1kw. And for whatever reason it is drawing from the battery even though the 4kw of solar coming in is plenty for everything. My sense energy monitor and AP systems portal are in agreement about my solar production, but it sees the solar input as a load?
RIght now I've got the CTs installed on grid side of the main breaker. I've also tried having them installed on the grid connection at the inverter itself, which more or less produces the same behavior.
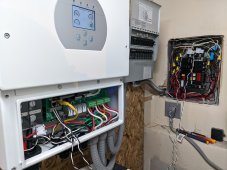
I suspect this is due to the way that things are wired connected at my MSP, but I'm not sure how to resolve it. Or maybe it's because I'm using the grid input as my solar input (manuals say this is correct, but maybe the SW doesn't like it.)
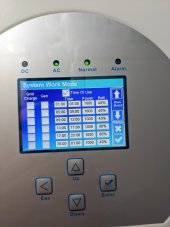
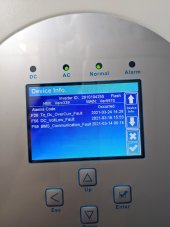
Last edited: