totalconfusion
New Member
- Joined
- Dec 24, 2020
- Messages
- 62
Comparison of "100A" fused distribution blocks: eBay VS Blue Sea
Sorry for all the pictures, I down scaled them but maybe not enough
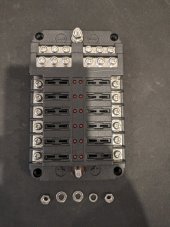
eBay

BlueSea
First off I love that these blocks have an integrated negative block, really clean and easy. I couldn't go back to individual blocks for positive and negative.
I don't know why they both chose to use 10-32 Studs (M5) It just seems really small. I think M6 or M8 would have been a better choice and make finding fittings easier for larger gauge wire.
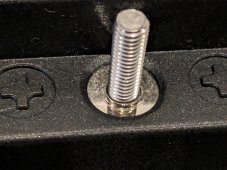
The conductor near the base of the studs on the eBay job are recessed in, making for what looks like a really shit/no touch connection.
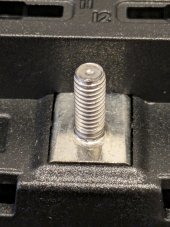
Blue Sea in comparison has a big flat surface to mount to
After deciding to toss the eBay block and find a better alternative is when I came across the Blue Sea product. It seems like it's the only real alternative out there. Is anyone using a different brand? They can't be the only company making blocks like this.
Sorry for all the pictures, I down scaled them but maybe not enough
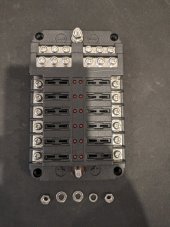
eBay

BlueSea
First off I love that these blocks have an integrated negative block, really clean and easy. I couldn't go back to individual blocks for positive and negative.
I don't know why they both chose to use 10-32 Studs (M5) It just seems really small. I think M6 or M8 would have been a better choice and make finding fittings easier for larger gauge wire.
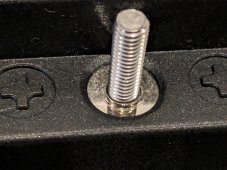
The conductor near the base of the studs on the eBay job are recessed in, making for what looks like a really shit/no touch connection.
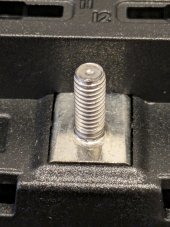
Blue Sea in comparison has a big flat surface to mount to
After deciding to toss the eBay block and find a better alternative is when I came across the Blue Sea product. It seems like it's the only real alternative out there. Is anyone using a different brand? They can't be the only company making blocks like this.