With a MPPT controller- series gives the best results ...
In terms of total power generation made per day, series gives the best results, then series parallel, then all in parallel comes in last- a series array on MPPT can see up to 20-30% over the exact same panels in parallel...
It comes down to charging voltages- unless you have one of the rarer (and more expensive) buck/boost MPPT ones, at lower voltages, the MPPT simply works as a PWM (giving the same low efficiency)- until your array voltage is usually 3-5v above the battery charge voltage, the MPPT part of the circuit is effectively bypassed and the panel voltage is what is charging the battery up
So your 'all in parallel' system has to get the panel voltages up (under load) to a minimum of about 18-20v on a 12v battery bank before the actual power matching starts to take place, so at that point they are running at a lower efficiency (and with some panels indeed a parallel array may NEVER get out of that low efficiency PWM range!!!) where a series array with say 3 panels- each panel only has to get to 1/3 of the charge voltage plus that 'bit extra' and the MPPT kicks into life...
Here's one of my own (I use it as an example so post it a bit)- its literally at dawn, suns not even up fully, no direct sun on the panels, and already 0.5A is flowing into the battery bank...
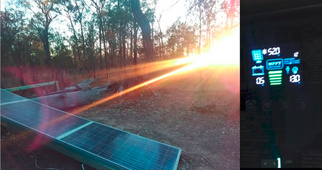
Because even under those conditions- each 30v Vmp panel in my series string only has to reach about 1/3 of that 13.8v + 3 to 5v (so say 18v in total) which means that each panel only has to hit about 6v from it, and the MPPT part can kick into life and start trying to maximise the yield, where all in parallel (especially 'low voltage panels' like the 18-20v Vmp like many buy to run in parallel) may not get to that same point for hours- at dawn, you can see that my array is already up at 50v- and the MPPT circuits are in operation already, sucking every last milliwatt of power they can from that arrays output... Sure its not a lot- but when you are offgrid- every last bit counts- and that extra hour or two before a PWM finally gets enough voltage under load to start producing major power, a high voltage series MPPT will have already been putting power (at reduced levels yes) for a couple of hours...
And in poor weather conditions, the MPPT will stay keeping on trying its best (even with 100% cloud cover and showers) it will keep on using the higher voltage to pump as much charge as it can into the battery bank- a PWM or all in parallel array on a MPPT may never never rise high enough to put a substantial charge in all day in those conditions (if indeed any at all)
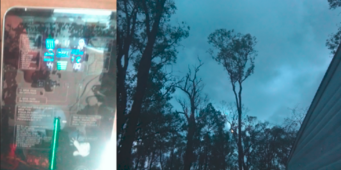
Here you can see (sorry about the reflections- it was that dark I had the lights on in the caravan lol) but that was 8AM, 100% grey cloud cover, with showers all day, and the sun still in the treetops (look for the arrow, its pointing at the 'bright spot' that is the sun) and that array is already putting 4.4A into the battery bank- a parallel array on PWM (or MPPT even) may never reach a point where it manages much if any charge all day- yet that system is already at about 10% of its normal maximum output (and will climb further once the sun clears the treetops... on days like that, I still hit 50% of my 'normal' output even with the cloud cover and rain...)
The higher the arrays voltage is, the lower the light levels needed before you can start charging (especially on a lower voltage battery bank)- this is why a MPPT should always be run as close as possible to its maximum voltage input level, consistent with its safety-you should NEVER be right at the PVmax rating on your controller- in certain weather conditions- your panels can exceed briefly their 'specs' rating by 10%-15%- and if you are already right at that voltage limit- well magic smoke comes out of the electronics (everyone knows electronics doesn't really run on on electricity, but smoke... when it comes out- electronics stop working lol). So my personal preference is to run the arrays combined Vocs at 80% of the PVmax rating of the controller- that way 'when' those specific conditions occur, smoke stays inside...
It is also why high voltage MPPTs (running in series) can even on good days, make up to 30% more total generated power per day in total compared to PWM or low voltage parallel MPPT- they start earlier and finish later than the low voltage stuff... same midday peak- but that really isn't that important- a short high peak means nothing if it doesn't even start generating until hours after one with a lower peak starts up- some fixate on maximising that peak- I look instead at maximising the total daily power made- and thats what runs your stuff- more daily power made means longer run times for your appliances lol
(My own system is a 150v PVmax controller, with 3 series panels rated at 30.43v Vmp and 38.17v Voc- in practice it runs about 90v in good conditions, but with their combined Voc's being 114.5v, 80% of 150v is 120v so even if the panels 'spiked' in output up to 15%, my controller is still safe with the array voltage only reaching 137.4v- had I had panels with a 44v Voc instead, their combined voc would have been 132v, add in a 15% spike and thats 158.4v- over the 150v PVmax- it 'may' survive' it 'may not'...
This is why selecting your equipment and matching specs is so important to making the best performing system that will be reliable and make the most power for the least $$$