AdamSmith73
New Member
- Joined
- Mar 11, 2020
- Messages
- 10
I really enjoy Will's education and leadership in the DIY solar and battery community. I have a small off-grid solar system (800w) powering my amateur radio shack, but before finding Will's YouTube channel, I didn't realize how mismatched and inadequate my 12v Pb-acid AGM 200AH battery bank was. So after watching his and others' videos - I decided to jump in with both feet and I am in the process of assembling two 3.3kWH 48v LiFePO4 battery packs that will be paralleled and charged by my Morningstar TS-MPPT-45 charge controller. I am still waiting on many of the critical parts (like the BMSs) to arrive from Aliexpress.com with the COVID-19 delays, but things are shaping up well. I am using A123 LiFePO4 cells harvested from the NEC battery packs BatteryHookup.com has been selling for some time.
I have learned a ton and am still learning every day as I work through new design and troubleshooting challenges as I built these batteries from scratch - using Will's book and great videos! Here are some pics of the project in progress... The two Gator cases will each hold a 3.3kWH 48v pack.
I will post updates as I slowly put things together and test.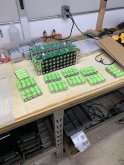
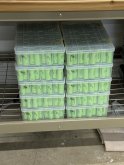
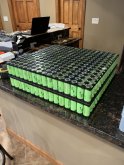
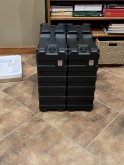
I have learned a ton and am still learning every day as I work through new design and troubleshooting challenges as I built these batteries from scratch - using Will's book and great videos! Here are some pics of the project in progress... The two Gator cases will each hold a 3.3kWH 48v pack.
I will post updates as I slowly put things together and test.
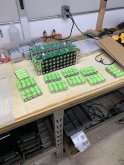
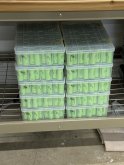
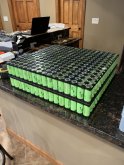
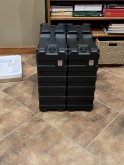