No danger with the bms, it’s just an error in state of charge reporting. As far as I can tell everything else about it works, like balancing. It simply never gets to a harmful voltage. My solar assistant looks at the three batteries and averages the state of charge so now when I look at the dashboard I never see 100% even though it is. I ordered another bms, the same as the two that work and learn (24S) they are cheap enough to be considered disposable so I might even get one more. Just want the right data.
The voltage received at the batteries are all within .002mv with a 20 amp load and loss through the bms is equal so it’s swap out time in a few weeks. NBD!
Helicoils are a bit labor intensive and costly, from a production standpoint. The use is primarily repair of bad or wrong threads, improve thread longevity for repetitive use of fasteners in soft material like pure copper, aluminum(non-alloy) or plastic. It could be you have a more pure alloy(softer) that makes it easier and better to weld to the battery post which I know is very soft and low alloy. I’ve installed hundreds of Helicoils and Keenserts mostly the latter. But I prefer the Helicoils. They get a bad rap because the installer doesn’t knock out the tang or does it wrong. Omitting it leads to it peeling out or locking up the fastener. Just glad you didn’t use those short bolts. Grub screws/set screws are the way to go.
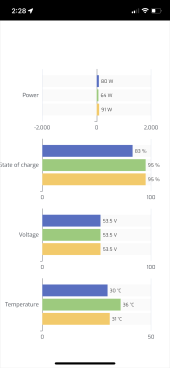
The voltage received at the batteries are all within .002mv with a 20 amp load and loss through the bms is equal so it’s swap out time in a few weeks. NBD!
Helicoils are a bit labor intensive and costly, from a production standpoint. The use is primarily repair of bad or wrong threads, improve thread longevity for repetitive use of fasteners in soft material like pure copper, aluminum(non-alloy) or plastic. It could be you have a more pure alloy(softer) that makes it easier and better to weld to the battery post which I know is very soft and low alloy. I’ve installed hundreds of Helicoils and Keenserts mostly the latter. But I prefer the Helicoils. They get a bad rap because the installer doesn’t knock out the tang or does it wrong. Omitting it leads to it peeling out or locking up the fastener. Just glad you didn’t use those short bolts. Grub screws/set screws are the way to go.
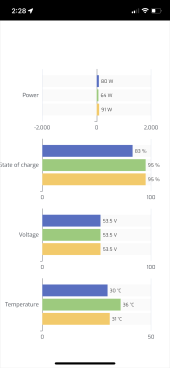