curiouscarbon
Science Penguin
- Joined
- Jun 29, 2020
- Messages
- 3,022
have considered a brushless electric motor as alternator? available from hobby store for rc car rc boat rc plane
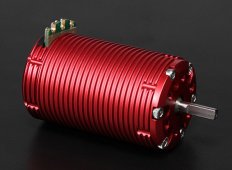
this one, a 2100KV (kilo rpm per volt metric) sensored brushless motor with max power rating 2000W
hobbyking.com
i’m using it to experiment with making a fan lol. so the inverse of what you’re doing.
but anyways, maybe a motor like this could be used in “regen” mode as the alternator?
it has three power conductors
and six sensor conductors
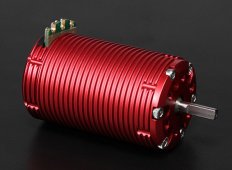
this one, a 2100KV (kilo rpm per volt metric) sensored brushless motor with max power rating 2000W
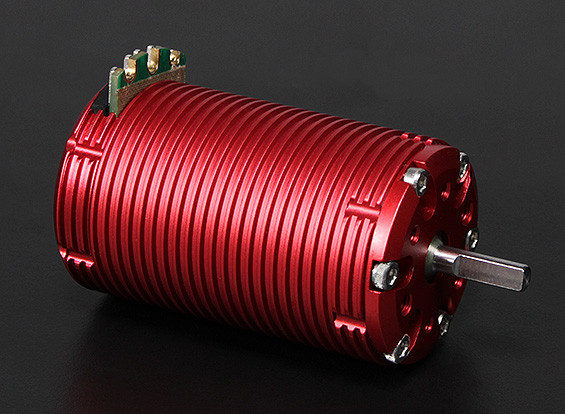
Turnigy TrackStar 2100KV 1/8th Sensored Brushless Motor
Turnigy TrackStar 1/8th Sensored Brushless Motor 2100KV
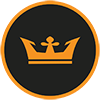
i’m using it to experiment with making a fan lol. so the inverse of what you’re doing.
but anyways, maybe a motor like this could be used in “regen” mode as the alternator?
it has three power conductors
and six sensor conductors
Poles: 4
Sensored: Yes (Standard 6 pin harness)
Max voltage: 15V (4S)
Max Current: 140A
Max Watts: 2100W
Resistance: 0.007ohm
Shaft Size: 5mm
Can Diameter: 42mm
Can Length: 70mm
Weight: 329g