I'd like to validate my idea of top balancing of battery pack with BMS 1A balancer only.
My setup is 16s EVE LF280K and B1A20S15P JK BMS which provides 1A balancing current. Iverter is Axioma Energy BFP5600 which is known as Axpert/Voltronix 5600 version. Initially all cells were at ±3.3v and, as expected, they are not balanced.
I read almost all forum topics on balancing and know the recommeded procedire. Still, I decided to skip top balancing wih power supply for two reasons. First, I do not have access to one and cannot wait for it to ship (I also build the battery for myself so probably this would be the only single use of that PSU). Second, I want to connect and use the batteries ASAP, even not finely balanced. As of now here in Ukraine we have grid electricity 4 hours on / 8 hours off or vice versa, because terrorist state of russia destroyed big part of or grid infrastructure with missiles...
Back to my idea.
1. Set BMS cell top at 3.6v (recoery at 3.55v), start balance at 3.45
2. Set invertor voltage to 54.2v (3.375*15 + 3.55) - when during charging the first cell goes to 3.5v, others are around 3.375
3. With time, more cells go to higher range, so I gradually increase the invertor voltage until it reaches 56v (3.5*16)
I expect it to finish balancing in day or two from now.
Initial state (less than 1d of runtime)
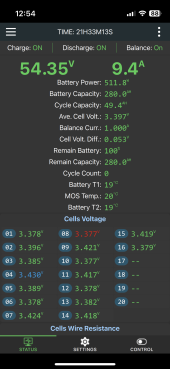
And now (almost 4d running) - 8 cells already over 3.5 and diff is 0.123v
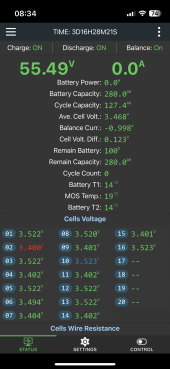
My setup is 16s EVE LF280K and B1A20S15P JK BMS which provides 1A balancing current. Iverter is Axioma Energy BFP5600 which is known as Axpert/Voltronix 5600 version. Initially all cells were at ±3.3v and, as expected, they are not balanced.
I read almost all forum topics on balancing and know the recommeded procedire. Still, I decided to skip top balancing wih power supply for two reasons. First, I do not have access to one and cannot wait for it to ship (I also build the battery for myself so probably this would be the only single use of that PSU). Second, I want to connect and use the batteries ASAP, even not finely balanced. As of now here in Ukraine we have grid electricity 4 hours on / 8 hours off or vice versa, because terrorist state of russia destroyed big part of or grid infrastructure with missiles...
Back to my idea.
1. Set BMS cell top at 3.6v (recoery at 3.55v), start balance at 3.45
2. Set invertor voltage to 54.2v (3.375*15 + 3.55) - when during charging the first cell goes to 3.5v, others are around 3.375
3. With time, more cells go to higher range, so I gradually increase the invertor voltage until it reaches 56v (3.5*16)
I expect it to finish balancing in day or two from now.
Initial state (less than 1d of runtime)
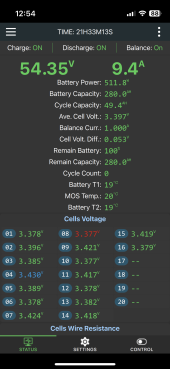
And now (almost 4d running) - 8 cells already over 3.5 and diff is 0.123v
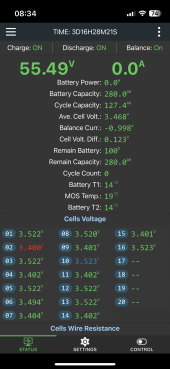