Life Expectancy Chart of Aluminum Lithium Batteries
Posted by Carl Clark on 8/20/2018 to
Lithium Battery Info
Aluminum Encased Batteries Have TWICE the Life of Plastic Encased Batteries
Measuring the life expectancy of a lithium battery is difficult to pinpoint. So we thought that we would like to expound on the subject to help an anticipated lithium user understand the issue and conclude how to get the maximum life from their battery pack.
Understanding Charge Cycle Life – Lithium vs. Lead Acid
Typically the life of any battery is measured in the number of charges the battery has before it deteriorates to a point where it can only hold 80% of its capacity when it was new. This number is called the batteries ‘Charge Cycle Life’.
As a comparison I would like to start with a lead acid battery. Lead acid batteries have a charge cycle life of between 350 charges all the way up past 600 charges. With the lower charge cycle life usually found in car starter batteries and the higher charge cycle life found in laboratory or solar storage applications. But here is where things can become a little misleading. The honest way of measuring a battery’s life can be manipulated. Because of the
Peukert effect which exists on all lead acid batteries you cannot discharge more than about 55% of the batteries new 20 hour capacity rating. A 100 Amp Hour ‘Ah lead acid battery will only yield about 55 Ah before it is considered fully discharged.
Lithium batteries are not affected by Peukert’s Law to the extent that lead acid batteries are so you can discharge a lithium battery down to 20% of its full State of Charge ‘SOC’ before the battery is considered discharged. With many lithium batteries if the discharge is more that 80% DOD it will not hurt the batteries life but is generally accepted that the lithium battery is fully discharged at 80% DOD. To run honest tests to determine the exact life of a lithium battery the battery must be fully charged and then fully discharged to 80% DOD.
Charging and discharging thousands of times takes a lot of time therefore most companies will do it for a number of complete cycles and then extrapolate the remaining life expectancy based upon some typical known curves for the chemistry of the battery.
Lithium Titanium Cells and Polymer Battery Drawbacks
Lithium Titanium cells have the longest life. But they are 3 to 5 times more expensive than the common Lithium Iron Phosphate ‘LiFePO4’ battery. Lithium Nickel Cobalt Magnesium (also called a polymer battery) or NCM batteries exhibit about half the life of the LiFePO4 cells. NCM batteries are lighter in weight and lower in cost and are often seen in electric vehicle applications where cost and weight are paramount.
How Companies Cheat on Charge Cycles
Some companies cheat and they say that their LiFePO4 batteries will last over some ridiculous number - like 8000 charge cycles. Those numbers are not realistic if they fully discharge the battery down to 80% DOD, which they do not. However, there are several other factors that play into the battery life scenario. One of them is the case of the battery. When batteries charge or discharge they create heat. Heat that is trapped inside the battery will cause the battery life to go down. A plastic encased battery of a given Ah rating will have a shorter life than a metal encased cell. That is because the plastic is a poor thermal conductor.
The smaller the Ah rating of the battery the easier it is for the battery stack to dissipate the heat away from the core of the stack and therefore will have a longer life. Honest manufactures of LiFePO4 plastic encased batteries which I call a prismatic cell will normally claim that their cells will have more than 2000 charge cycles. A prismatic plastic encased battery is illustrated in the graph that is in this dissertation.
Why Aluminum Encased Lithium Batteries Perform Better
A typical aluminum encased battery that has better heat dissipation will start out higher. Dependent upon the size of the cell the expectant charger cycle life of a smaller LifePO4 cell can be as much as 4000 charge cycles and follow the same trajectory of the plastic prismatic cell shown below. The simple fact is that if you have an application where you want a long life, like for solar storage, and you do not discharge the cells below their nominal 3.2 voltage you will have a cell that will probably outlive you. Depth of discharge has a very profound effect on a lithium battery’s life.
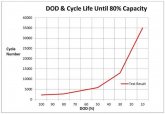
What is the Life Expectancy of the
Aluminum Batteries?
- Factor 1: Depth of Discharge…Percentage of Capacity Used Per Cycle.
- DOD, short for the Depth of Discharge, is used to describe how deeply the battery is discharged. If we say a battery is 100% fully charged, it means the DOD of this battery is 0%, If we say the battery have delivered 30% of its energy, here are 70% energy reserved, we say the DOD of this battery is 30%.
- Factor 2: Discharge Rate, The AMPS Divided by the Capacity
- To Read the Chart Above, Here are Some Examples
A. All Numbers are at a 1C Discharge Rate, Which is Aggressive…
B. At a 90% Depth of Discharge, Our Batteries Will Provide 2400 Cycle to 80% State-of-Original-Capacity (SOIC)
C. At a 10% Depth of Discharge (Say, Engine Starting) Our Batteries Will Provide 35,000 Cycles Until 80% SOIC. Beyond 35,000 Cycles the Battery is Still Functioning But Gradually Losing Capacity, but not Performance
Conclusion: By recharging a lithium battery more frequently, thus reducing the DOD (depth of discharge), the battery cycle life is Increased. Solar is very often a beneficial method to reduce DOD and increase life!