Both 6061 and 6063 are structural with nearly identical strength coefficients.
6063 has better corrosion resistance.
Corrosion resistance is the primary reason to use them. I live in Florida and my cells will be in the camper in the heat and humidity constantly. A 10+ year life cycle means that there is plenty of time for corrosion to set in.
When, noy if, galvanic corrosion starts, I want it to be somewhere I can see it and not removing the threads from my cells, which is exactly what will happen first with a steel bolt.
www.thomasnet.com
6063 has better corrosion resistance.
Corrosion resistance is the primary reason to use them. I live in Florida and my cells will be in the camper in the heat and humidity constantly. A 10+ year life cycle means that there is plenty of time for corrosion to set in.
When, noy if, galvanic corrosion starts, I want it to be somewhere I can see it and not removing the threads from my cells, which is exactly what will happen first with a steel bolt.
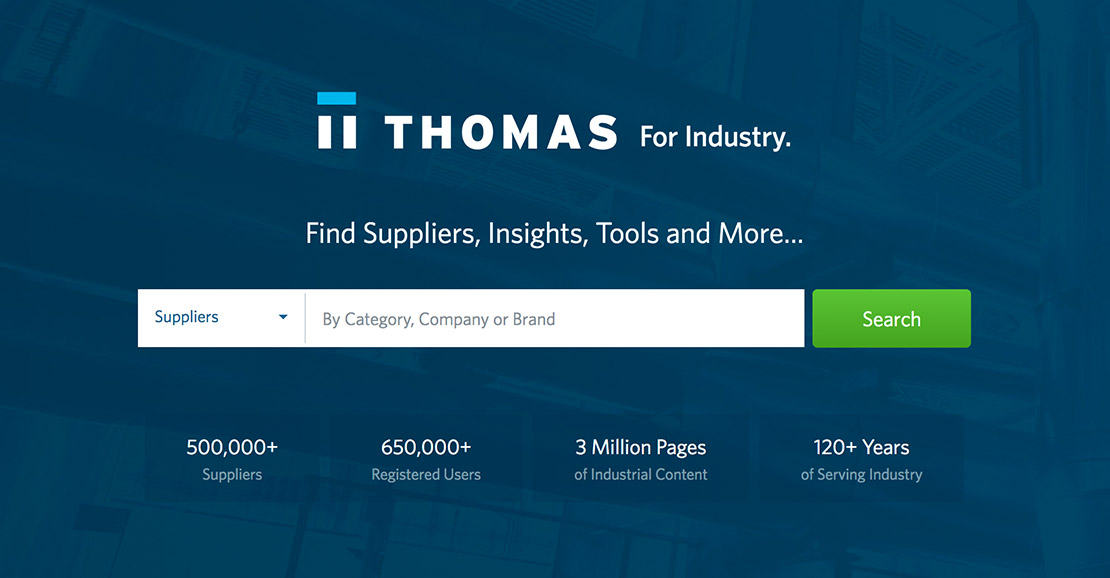
6061 Aluminum vs. 6063 Aluminum - Differences in Properties, Strength and Uses
This article presents a brief comparison of the properties, strength, and applications between 6061 and 6063 aluminum.