chrisski
Solar Boondocker
- Joined
- Aug 14, 2020
- Messages
- 5,192
I am wondering if anyone has installed 24 VDC in a fifth wheel or travel trailer, and how they got their 12 VDC to include electric brakes to work?
The intent of the 24 VDC install is to provide 1200 watts of panels to safely power a 2000 watt inverter. Unfortunately, everything else in the RV to include internal lighting and brakes would be powered by 12 VDC still. I 've seen DC to DC converters by Victron, and something like that would definitely work for all the 12 VDC appliances in the RV except the brakes.
I'm unsure how much power the brakes draw, but I do know they need a battery to operate. If the trailer battery is dead, the wiring from the 7 pin harness won't provide enough juice, and when the trailer battery is completely dead, the tow controller will read "Not Connected," and all braking definitely comes from the truck and not the trailer, as I found out driving with a dead battery. Because of not knowing the surge rating of my brakes, I'm reluctant to simply use a 24 VDC to 12 VDC converter and end up in a no brake situation.
==================
EDIT 21 Dec 2021 (A lot of good stuff in this thread including a buck converter that did not work, but here is what I used.
I just finished my 24 volt upgrade and got rid of the 12 volt battery. I installed a single Victron Orion 24 volt DC to 12 Volt DC converter 70 amp converter and things are fine. I have a 2 axle 12,000 LBS fifth wheel and that converter can operate the leveling system which pulls 50 amps at 12 volts and has no problem doing it.
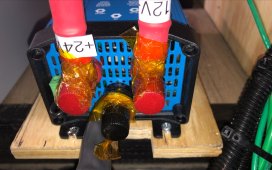
The intent of the 24 VDC install is to provide 1200 watts of panels to safely power a 2000 watt inverter. Unfortunately, everything else in the RV to include internal lighting and brakes would be powered by 12 VDC still. I 've seen DC to DC converters by Victron, and something like that would definitely work for all the 12 VDC appliances in the RV except the brakes.
I'm unsure how much power the brakes draw, but I do know they need a battery to operate. If the trailer battery is dead, the wiring from the 7 pin harness won't provide enough juice, and when the trailer battery is completely dead, the tow controller will read "Not Connected," and all braking definitely comes from the truck and not the trailer, as I found out driving with a dead battery. Because of not knowing the surge rating of my brakes, I'm reluctant to simply use a 24 VDC to 12 VDC converter and end up in a no brake situation.
==================
EDIT 21 Dec 2021 (A lot of good stuff in this thread including a buck converter that did not work, but here is what I used.
I just finished my 24 volt upgrade and got rid of the 12 volt battery. I installed a single Victron Orion 24 volt DC to 12 Volt DC converter 70 amp converter and things are fine. I have a 2 axle 12,000 LBS fifth wheel and that converter can operate the leveling system which pulls 50 amps at 12 volts and has no problem doing it.
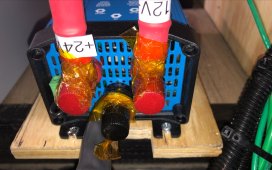
Last edited: