I have a 24v 230ah LiFePo4 battery pack made from 8s 3.2v 230ah cells from Docan Technology through Jenny Wu with a JBD 150a BMS. When they arrived a while ago I checked that the voltages of each cell are near identical, and from some suggestions, top balancing isn't necessary if they are new and the same voltages.
However I have a problem when the battery pack is fully charged or near 230ah, two of the cells have much higher voltages than the rest according to the BMS. Below is what I see on the JBD BMS Bluetooth app:
Normal, not fully charged(also very similar voltage difference when charging):
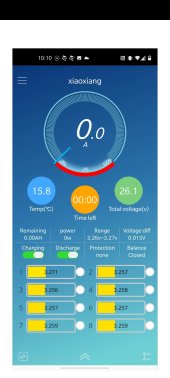
Cells 2 and 4 higher voltage when fully charged:

Does this mean I have top balance all the cells? I had thought that if the cells are tested from the manufacturer, are grade A, and have the same voltages when they receive and test them, then they should be balanced?
However I have a problem when the battery pack is fully charged or near 230ah, two of the cells have much higher voltages than the rest according to the BMS. Below is what I see on the JBD BMS Bluetooth app:
Normal, not fully charged(also very similar voltage difference when charging):
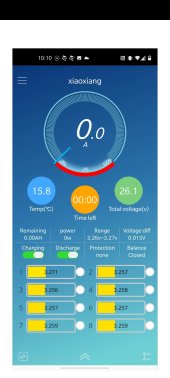
Cells 2 and 4 higher voltage when fully charged:

Does this mean I have top balance all the cells? I had thought that if the cells are tested from the manufacturer, are grade A, and have the same voltages when they receive and test them, then they should be balanced?