I worked on solving the issue with the 2 groups of cells that had high resistance and high voltage fluctuations as seen by the BMS. I solved it, and I'm in shock.
To recap - under load I would see about 4x the resistance between cell groups 4 and 5 (and between 12 and 13). It didn't show for the groups between 8 and 9 because the 9th group has its own negative BMS cell tap so the resistance between cells 8 and 9 don't get caught in the long cable joining the two. The BMS shows this as the yellow and green lines for cells 5 and 13:
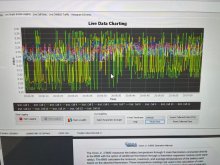
This was causing the BMS to prematurely think that it was time to balance the cells, caused bad SoC corrections, and was providing erratic voltage readings for the entire battery (which was making the Quattro's constantly adjust the charging). I needed to solve this problem.
I tried using the Orion bus bar compensation feature (you manually add the resistance of the wire) which should correct for this -- but it didn't. I was having a hard time believing this could be skin effect, so my next attempt was to replace the two long 1 gauge cables with a single short 3/0 cable. No improvement. So, the only thing left to try was a bus bar. Fortunately I had the 1/4" by 1" tinned copper bars that I never really used and I notched out the wood and gave that a try between cell groups 4 and 5. I'm so grateful I have a drill press and chop saw now! That made this relatively easy:
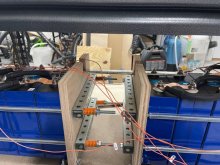
and here's the result:
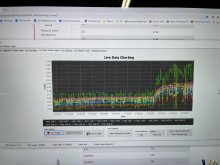
I couldn't believe my eyes! The yellow line is with the others and the only outlier is the green line (cell 13). Here's a clearer view with just cells 4, 5, and 13 selected:

OK, so 5 is a little higher than 4 -- which might seem expected but I measure half the resistance (half the voltage drop as seen by my meter) across that mammoth copper bar (it's more copper than 4/0), so I'm not sure what that's all about -- but it's quite clear that cell 13 is ridiculous. Here's the calculated resistances according to the Orion BMS - notice cell 13 is crazy high. Cell 5 is higher than the others -- which does not agree with my meter, so that's weird.
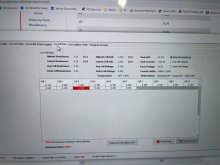
So I replaced both connections - and here's my charge completing:
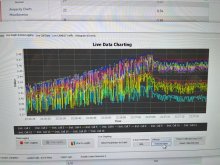
SO much cleaner.
The downside of this is the physical stress that might be happening on the terminals while driving down the road. I'm now starting to contemplate going to groups of 16 and forgoing the individual mobility of each pack.
Given that the distance between the terminals is moving 0.2mm at most, I'm going to go back to solid bus bars (the same 1/4" by 1" stuff). I'm also ordering some 1/16" by 1" copper so I can attempt bending some copper in order to make the connections from the main battery positives and negatives to the contactor and circuit breaker rather than using wire (not due to the skin effect, but due to space constraints of trying to route the cables to the board directly to the right of the top and bottom rows of the battery, below).
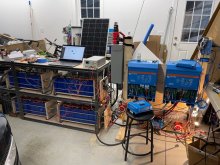
To recap - under load I would see about 4x the resistance between cell groups 4 and 5 (and between 12 and 13). It didn't show for the groups between 8 and 9 because the 9th group has its own negative BMS cell tap so the resistance between cells 8 and 9 don't get caught in the long cable joining the two. The BMS shows this as the yellow and green lines for cells 5 and 13:
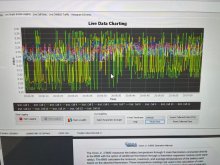
This was causing the BMS to prematurely think that it was time to balance the cells, caused bad SoC corrections, and was providing erratic voltage readings for the entire battery (which was making the Quattro's constantly adjust the charging). I needed to solve this problem.
I tried using the Orion bus bar compensation feature (you manually add the resistance of the wire) which should correct for this -- but it didn't. I was having a hard time believing this could be skin effect, so my next attempt was to replace the two long 1 gauge cables with a single short 3/0 cable. No improvement. So, the only thing left to try was a bus bar. Fortunately I had the 1/4" by 1" tinned copper bars that I never really used and I notched out the wood and gave that a try between cell groups 4 and 5. I'm so grateful I have a drill press and chop saw now! That made this relatively easy:
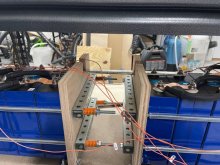
and here's the result:
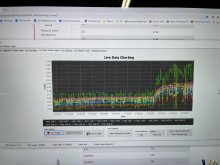
I couldn't believe my eyes! The yellow line is with the others and the only outlier is the green line (cell 13). Here's a clearer view with just cells 4, 5, and 13 selected:

OK, so 5 is a little higher than 4 -- which might seem expected but I measure half the resistance (half the voltage drop as seen by my meter) across that mammoth copper bar (it's more copper than 4/0), so I'm not sure what that's all about -- but it's quite clear that cell 13 is ridiculous. Here's the calculated resistances according to the Orion BMS - notice cell 13 is crazy high. Cell 5 is higher than the others -- which does not agree with my meter, so that's weird.
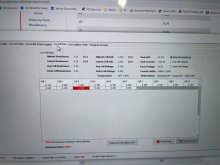
So I replaced both connections - and here's my charge completing:
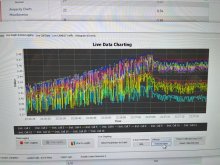
SO much cleaner.
The downside of this is the physical stress that might be happening on the terminals while driving down the road. I'm now starting to contemplate going to groups of 16 and forgoing the individual mobility of each pack.
Given that the distance between the terminals is moving 0.2mm at most, I'm going to go back to solid bus bars (the same 1/4" by 1" stuff). I'm also ordering some 1/16" by 1" copper so I can attempt bending some copper in order to make the connections from the main battery positives and negatives to the contactor and circuit breaker rather than using wire (not due to the skin effect, but due to space constraints of trying to route the cables to the board directly to the right of the top and bottom rows of the battery, below).
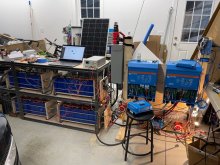