I have read from several experienced users that it is wise to derate FET based BMS current ratings by 50%. I was wondering if anyone has any experience with adding cooling to a BMS that they would be willing to share? Does enhanced cooling capability increase the usable current rating of a FET based BMS or is there some other limiting factor that is going to kick in first (like the 6AWG wires that came on my "150A" Daly BMS).
I just purchased this 300A Heltec BMS and its construction makes me think there is actually a prayer of it handling a reasonable fraction of its current rating (at least the cable connections provided hint this might be the case).
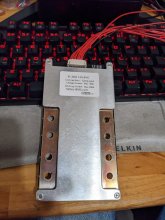
I bought two of these passive server CPU coolers for another project and ended up not using them. I should be able mount one or both (one on each side) on the Heltec BMS without difficulty. Once I get my 280 AH battery pack put together I plan on doing some experimentation to see how much difference in heat rise I get in the BMS with and without heatsinks. I really hope this Heltec BMS are not a disappointment. I don't see myself actually needing to draw 300A from the battery pack, but heat is the enemy to a long and happy life `when it comes to electronics.
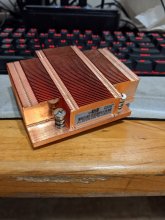
I just purchased this 300A Heltec BMS and its construction makes me think there is actually a prayer of it handling a reasonable fraction of its current rating (at least the cable connections provided hint this might be the case).
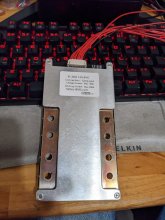
I bought two of these passive server CPU coolers for another project and ended up not using them. I should be able mount one or both (one on each side) on the Heltec BMS without difficulty. Once I get my 280 AH battery pack put together I plan on doing some experimentation to see how much difference in heat rise I get in the BMS with and without heatsinks. I really hope this Heltec BMS are not a disappointment. I don't see myself actually needing to draw 300A from the battery pack, but heat is the enemy to a long and happy life `when it comes to electronics.
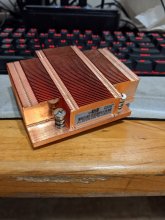